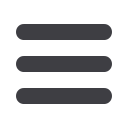
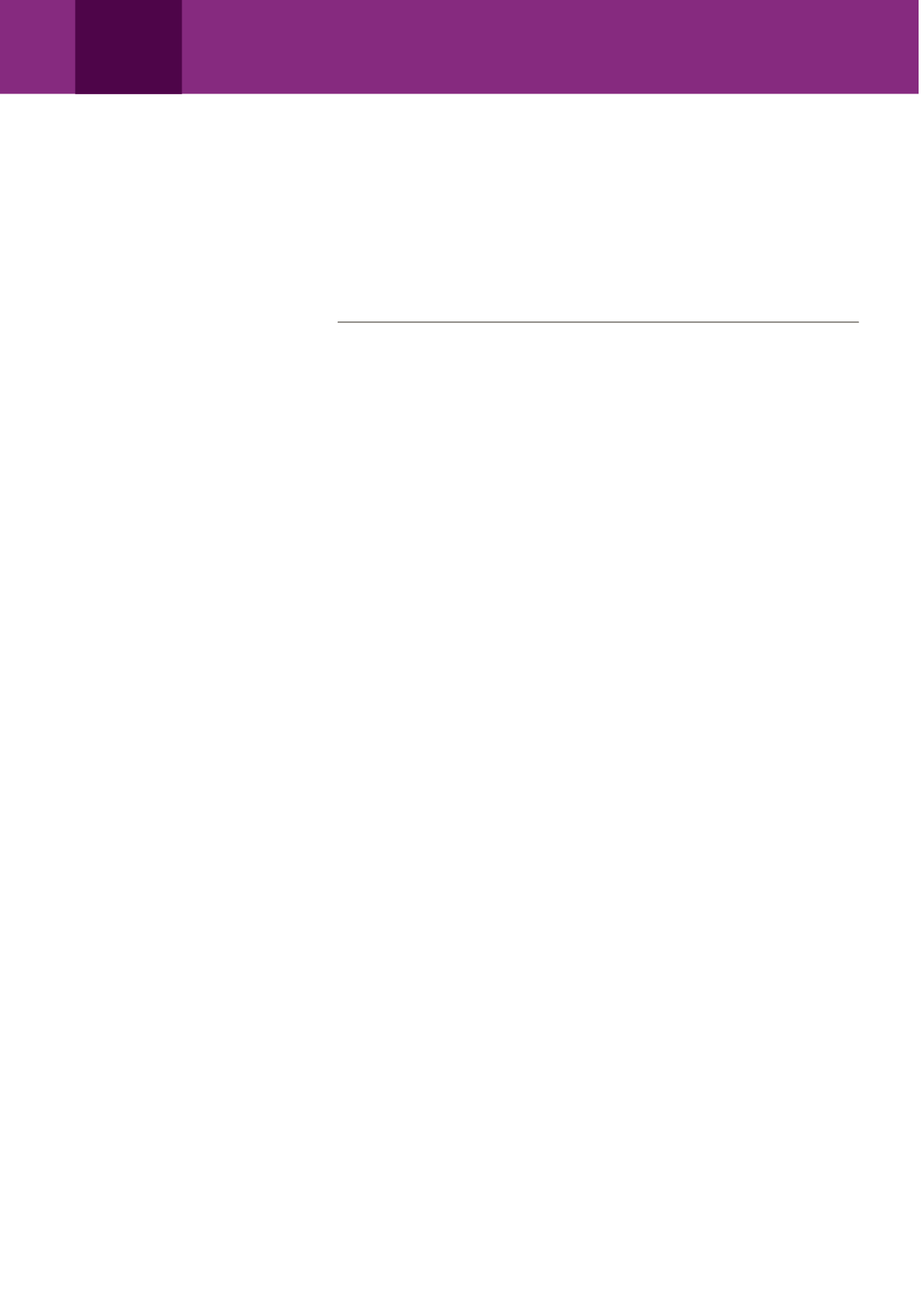
Technical article
March 2015
86
www.read-eurowire.comLong-term cable reliability
design criteria
By David Mazzarese, Mike Kinard and Kariofilis (Phil) Konstadinidis, OFS, Norcross, Georgia, USA
Abstract
This paper investigates the current
requirements for allowable axial load on
optical cables. It is shown that the current
criterion found in many optical cable
standards – that the allowable long-term
load should be less than 20 per cent of
the proof test stress – may be optimistic
in some cases. Instead, a new criterion –
that the long-term load be standardised as
0.14 GPa (20 kpsi) – is recommended.
1 Introduction
In overhead cables, there is a set of
conflicting design requirements that must
be optimised. One objective is to minimise
the strain on the optical fibres. A second
objective is to minimise the cable diameter
to reduce wind and ice loading. A third is
to minimise the sag in each span.
Aramid yarn added to the cable minimises
strain and sag, but the added material
increases the diameter of the cable, which
in turn increases the wind and ice loading.
One key variable in the optimisation of
these parameters is the allowable strain on
the optical fibre. A common rule of thumb,
which has been used for years, is to allow
a maximum of 20 per cent of the proof test
stress as a long-term strain on the optical
fibres in the cable.
This criterion appears in many of the
current standards documents and has
proven to be reasonable for the current
generation of cables manufactured with
0.69 GPa (100 kpsi) proof-tested fibre.
The criterion, which was developed to
provide 30-year mechanical reliability and
is based on the excellent overall reliability
performance of deployed overhead cables,
appears sound.
With cables being developed closer to
their design limits, it is worth exploring
these limits and the rules of thumb that
are used in cable design to ensure that,
in the future, deployed optical cables
will provide similar or better reliability
performance than their predecessors.
2 Impact of modified
cable designs on
reliability
2.1 General observations
The traditional design boundaries for
the manufacture of optical cables have
changed in the past ten years. Some of
these changes include:
1 Deployment of higher fibre count
cables
2 Deployment of low macro bend loss
fibres (G.657) and micro bend-resistant
coatings
3 Cutting costs by minimising material in
the cable and reducing design margins
4 Higher proof-tested fibres (1.38 GPa
[200 kpsi])
These changes in cable design trends can
impact the overall reliability of optical cables.
Each will be discussed separately to show
that, when combined, they could have a
dramatic impact on long-term reliability if
not managed correctly.
2.2 Deployment of higher fibre counts
Many overhead cables fall into the drop
cable category. These small cables tie the
access network to an individual dwelling.
These are typically low fibre-count cables.
Excluding these drop cables, however,
there is a general trend to deployment of
higher fibre-count cables. This is driven
by the high cost of rights of way and
installation.
In many higher fibre-count cables, half the
weight of optical cables comes from the
optical fibres. The higher weight requires
higher tension on the cable to minimise
cable sag. Aramid yarns and fibreglass
composites (FRP) are used to carry the
bulk of this load, with the residual load
being taken up by the optical fibres.
Further, the more fibres in an optical cable,
the larger its diameter becomes. Larger
diameter cables have greater wind- and
ice-loading, making the situation more
difficult. As a result, higher fibre-count
cables have the potential for more strain
on the optical fibres.
2.3 Deployment of G.657 fibres and
micro bend-resistant coatings
It is no surprise that we are seeing greater
deployment of G.657 fibres in the optical
network. Recent data from CRU has shown
that more than six per cent of optical
fibre being deployed today falls into this
category. [Private communications Patrick
Faye of CRU.] The G.657 fibres are being
deployed because of their superior macro
bend performance. One further benefit of
G.657 fibres is the improved micro bend
performance, making them less sensitive
to cabling conditions.
Another key development in optical fibres
is the deployment of micro bend-resistant
coatings
[1]
. This new generation of
optical coatings show two to four times
improvement in loss due to micro
bending, as compared to those deployed
five to ten years ago. Together, these two
improvements to the optical fibre have a
huge impact in observed cable attenuation,
even under aggressive conditions. The
superior fibre and coating properties can
‘mask’ the impact of a poor cable design or
installation.
When optical cables using traditional
G.652 fibres are deployed with high
residual strain on the fibre, higher
attenuation is often observed. By default,
the cable manufacturer is required to
control the strain on the fibre to ensure
the cable can meet the qualification
requirements.
When G.657 fibres with micro bend-
resistant coatings are used for the
same cable design, then the measured
attenuation will improve and the same
cable design may pass this optical
requirement. The net result of using
G.657 fibres is that the cable will pass
this qualification test. However, after
deployment, higher fibre strain could pose
a long-term reliability risk.
In short, if the cable is designed properly,
G.657 fibres and micro bend coatings are
a huge benefit to the optical performance
of the deployed cable. But if the cable is
designed poorly, the improved optical
fibres can mask the strain issue from the
end user, which could pose a long-term
mechanical reliability risk.