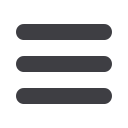
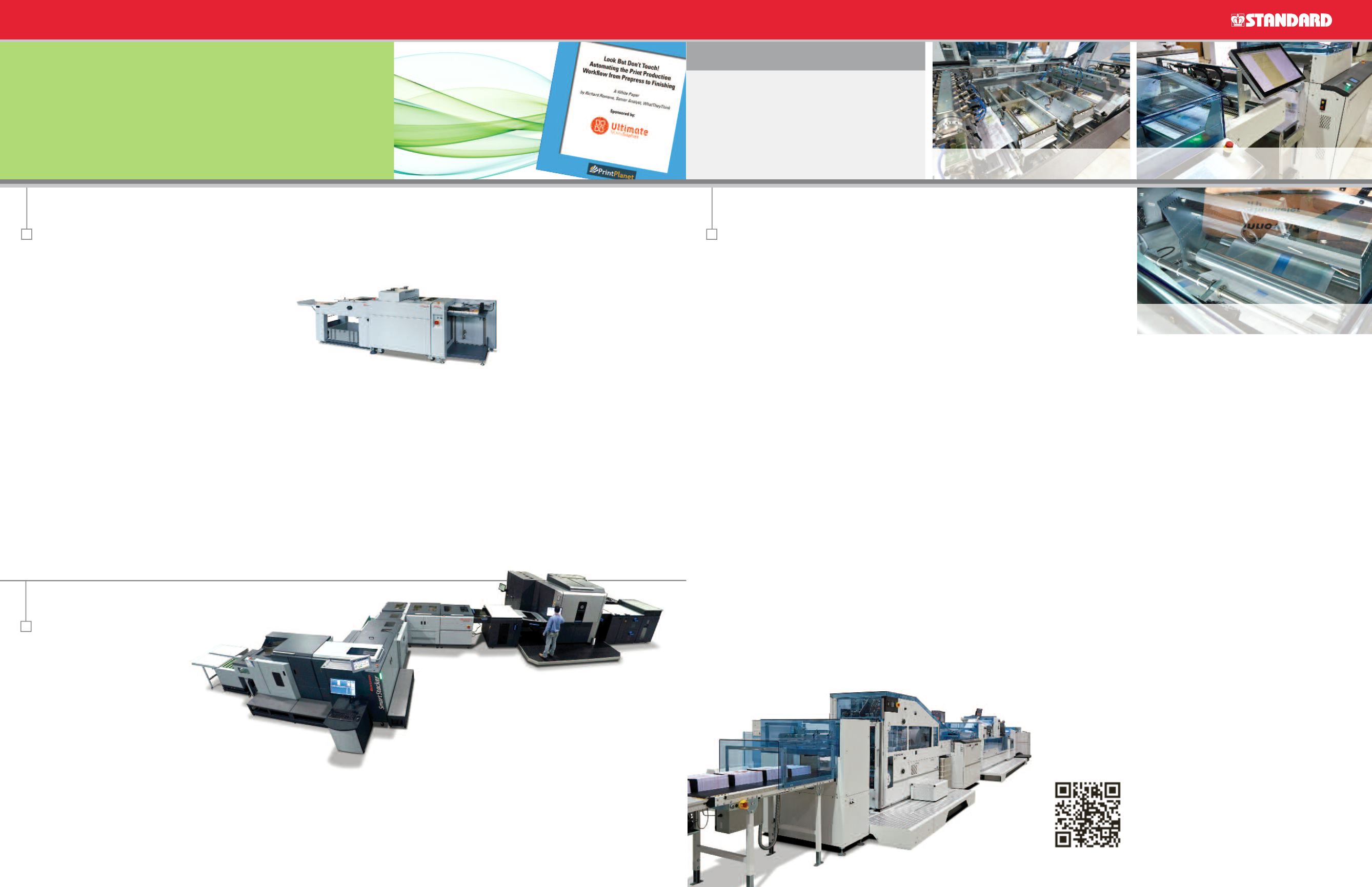
Look But
Don’t Touch!
Automating the
Print Production
Workflow from
Prepress to Finishing
Finish
Line
05.2015
6
A new white paper, written by industry analyst Richard Romano and
sponsored by Ultimate TechnoGraphics, is now available from PrintPlanet.
This paper explores the advantages of bindery automation and discusses
how new technologies are enabling this last piece of the production puzzle
to be included in an overall workflow automation system – allowing
complete, end-to-end “touch-free” print production.
To download the full whitepaper...
Visit
www.sdmc.com/whitepaperDie cutting has a long and rich history which dates back to the
1800s when it was originally used to cut and shape
leather for the shoe making industry. Since then, the
many varied applications for this process have ensured
its continued advancement throughout the years and
even today, the print market still profits from innovative
features that did not exist just a couple years ago.
Standard Horizon’s new line of rotary die cutters are
setting the bar for the next generation in die cutting,
with capabilities that simplify short-run die cutting while saving
time and money. When evaluating your die cutting requirements,
it’s important to consider the following technologies that can
bring added value to your bindery.
Repeat Register
The unique and patented repeat register function on the Horizon
RD Series of rotary die cutters significantly reduces the die cost
for many applications and provides additional flexibility. For
example, if a job has been printed three times down the sheet in
the direction of the feed, a die can be produced with a single
pattern on it that will strike the sheet three times in just one
pass – reducing die cost by as much as one third. Likewise, a die
that is produced for a 1-up job can be used to die-cut 1-up on a
9” x 12” substrate, or 2-up or 3-up on a 12” x 18” sheet – for
greater latitude during the design and print phases. If the gap or
Revolutionary features add flexibility and lower costs
Standard Horizon Rotary Die Cutters.
Nearly 2,400 industry professionals gathered to see the latest
digital print technologies amongst lively idea exchange and
networking at the recent Dscoop event in March, which
marked the tenth meeting of HP Indigo Users. In the HP
booth, the Standard Horizon SmartStacker was shown in-line
with the HP Indigo 10000 Digital Press. B2 size (20”x29”)
output from the HP press was automatically fed to the
SmartStacker and converted into as many as 28 full-bleed cut
Grows from 200 to over
2,000 attendees in ten year history.
Dscoop
2015
Annual conference in Washington, DC
sheets with intelligent accumulation and stacking, in one
single process. Book blocks were finished near-line on the
Standard Horizon BQ-280PUR Perfect Binder featuring book-
of-one production capability. The binder was enabled with HP
Direct2Finish software which allows fully automated finishing
set-ups and quick, error-free job changeovers by scanning a
job ticket. Standard also demonstrated solutions for die
cutting, creasing, folding, and three-knife trimming.
Tech Talk
I
Showtime Wrap-up
gutter between images on a multiple-up job varies, the repeat
pattern can be adjusted for
each image to ensure accurate
die cutting on all pieces.
Two Gap Settings
Patented technology on the
Standard Horizon RD-4055
Rotary Die Cutter allows you to
choose between two cylinder gap settings – either 0.8 mm or
1.0 mm – in a bearer to bearer system, which protects the die
from damage and also adds greater precision. This unique
feature provides two important advantages. First, it allows a
counter die to be mounted to the lower anvil cylinder for
creasing, embossing and debossing, which can be performed
simultaneously with the die cut. Second, it offers the ability to
choose between a 0.8 mm or less-expensive 0.6 mm flexible die
depending upon the job requirement.
Print Mark Register
Horizon die cutters can also be configured with Print Mark
Registration. This option allows registration to a print mark as
opposed to the leading edge of the sheet, and will automatically
adjust for digital print image shift from sheet-to-sheet to ensure
an accurate cut on every piece.
The Standard Horizon SmartStacker shown in-line with
the HP Indigo 10000 Digital Press.
Inspection, Tracking and
Reporting for Improved
Workflow
Of special note, the Hunkeler WI6 Web
Inspection system was shown as part of
the finishing lines in the Canon, HP,
Hunkeler and Xerox booths. The WI6
captured high resolution color images of
the full web for in-line verification, quality
inspection and integrity analysis of the
printed roll. This system can perform a
number of quality checks including color
tolerance, pattern matching, white space
verification, ink or toner spills, voids, jet-
outs, etc. and errored sheets can be
automatically diverted.
In addition, Hunkeler presented a new
sheet level tracking system for roll-to-stack
solutions. Sheets and sets can be tracked
throughout the entire line, thanks to a
combination of Datamatrix readers,
sensors and the internal registration and
drive control logic. Capabilities include
front to back matching, page sequence
control, and document and job
completeness. When combined with the
Hunkeler Site Manager, this solution will
also detect duplicates and missing
documents, track and report production,
and even generate reprints. Hunkeler’s
sheet level tracking solution improves
production workflow and efficiency at an
affordable price.
For more detailed product information,
photos, and video interviews, visit the
Innovationdays website at
http://innovationdays.hunkeler.ch/Lucerne was once again the global center
for "high performance digital printing" as
worldwide experts recently convened for
the eleventh Hunkeler Innovationdays.
This year’s event was the largest and
most diverse, with almost 6,000 visitors
traveling from over 50 nations, yet still
true to its unique and intimate character.
Standard was pleased to welcome an
impressive number of North American
customers to Switzerland earlier this year
including Quad/Graphics, RR Donnelley,
Shutterfly, Amazon, Bank of America,
and many more. Visitors saw many
exciting premieres demonstrating greater
automation and substrate flexibility,
including Hunkeler’s new generation of
unwinding and rewinding modules
featuring faster roll changes, 30” web
widths, and production speeds up to
1000 feet/minute. The event also
showcased book production solutions in
a variety of workflows, efficient
Finish
Line
05.2015
Showtime Wrap-up
Hunkeler Reports Successful
Innovationdays 2015.
Worldwide experts recently convened in Lucerne
Event serves as launching pad for several world premieres in
Inkjet Printing and Pre/Post Finishing.
Hunkeler premiered its DP8 Dynamic
Perforating module from the new POPP8
generation, which offers improved
productivity with even greater function-
ality and speed.
DP8 Takes Center Stage
Scan this code for a
360
°
view of the
Smart Binding System at
Innovationdays 2015!
7
A touchscreen editing tool on the DP8 allows fast
and easy set-ups.
The DP8 offers improved productivity for
dynamic perforation and punching.
Hunkeler’s new control platform enables end-to-
end control of print jobs.
The Hunkeler Plowfold Signature Book Block
production line delivers up to 4,140 96-page
books/hour in 6 x 9 format with multiple-up
book blocks on top of each other.
production of digitally printed brochures
with dynamic content and variable page
count, advanced laser finishing for
ultimate flexibility in dynamic perforating
and punching, and Hunkeler’s new
control platform enabling end-to-end
control of print jobs.
Among the highlights, Hunkeler
premiered its DP8 Dynamic Perforating
module from the new POPP8 generation,
which offers improved productivity with
even greater functionality and speed for
dynamic perforation and punching of
payment forms, tear-off coupons,
mailings and security applications.
Hunkeler also demonstrated its newly
enhanced Plowfold Signature Book Block
production line with variable format
sizes featuring fully automatic
longitudinal format changeover, high
flexibility, and excellent book block
quality.
Standard partner Horizon International
showcased a range of integrated
finishing solutions including the Smart
Binding System for perfect bound books.
This system produces short-run, variable
books of different sizes
and thicknesses
from a 20"-wide
roll with no
manual
touchpoints.