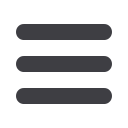

Institute of Measurement and Control. Functional Safety 2016
Page 9
During maintenance there may a requirement to change out a SIS sensor for an ostensibly equivalent
sensor from another manufacturer. With an Integrated approach any issues arising from differing
safety characteristics could be bought to the attention of maintenance staff thus avoiding a potential
problem.
The trend toward digitalisation is more than just having a common data model. Essentially the
combination of integrated engineering and integrated operations gives the ability to create a digital
version of the process plant along with its Industrial automation and control sometimes referred to as
a “digital twin”.
This digital twin will likely include a 3D spatial model of the plant which would traditionally have been
used for collision detection during initial design but, from a functional safety perspective, can also be
used, for instance, to help design and check the practicality of proof test procedures or for training
operators and maintenance technicians or for practising emergency evacuations. All of which could
help reduce the human error type systematic failures associated with proof testing, operations and
maintenance activities.
So long as we avoid distancing plant personnel from the process itself of in some way ‘gamifying’ the
serious business of running a potentially hazardous plant.
The other capability of a “digital twin” is the ability to automatically generate a model of the process
which can be used to test the automation and the SIS programming. Simulation per se is nothing new
but the ability to auto generate the simulation from the common data model helps avoid mistakes.
The ability to switch SIS controllers (and BPCS controllers) between operating with the simulation and
with the real plant without changing the code also reduces the potential for systematic errors. This
means the early stage verification testing is done on the exact same code as will eventually be
running in the SIS. Of course the validation of the safety system will still need to be done “in the real
world” but effective verification at the stage of testing can help reduce the time taken at FAT and SAT.
Integrated Operation
Integrated operation is intended to help optimise the plant during its operational life, which can be 40
years plus. It seeks to help tackle the challenges associated with plant downtime, increased flexibility,
cost, extensions, modernisation, legislation and safety. Increasing uptake in digitalisation means
newer technologies are being implemented at all levels of the plant hierarchy. Instrumentation is
getting smarter and makes more data available. Field buses and networks can pass this data through
the automation hierarchy across communications networks which are also increasing in bandwidth
and speed. This requires the tools to aggregate and analyse the data from a plant, site or enterprise
level and convert it into useful information and leads on to the topic of big data.
The adoption of Big Data has the potential to contribute to process safety in the following areas:-
Plant reliability and Asset Integrity
Steady state process control
Process Optimisation
Accident Investigation
Combining information from different silos (plants, sites, companies etc) for the purposes of
leading indicators for process safety
Using data from the BPCS and the SIS, maintenance systems and incidents to promote
process safety.
Allied with big data is the increasing use of the Cloud either as a means of consolidating Big Data or
as a way of providing Software as a Service (SaaS).