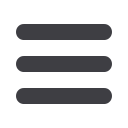

Paper 2: Why embrace the concept of the Safety Requirements Specification?
Institute of Measurement and Control – Functional Safety 2016
2
Process design.
Processes are designed in a structured environment with managed
processes and procedures, design reviews and modelling. Many process designs are
built from established elements using known and well understood techniques.
Automation design.
Once the basic control and safety requirements are established,
an expert team of discipline engineers will create an appropriate automation design.
Again, previous experience will guide the basic design.
System integration and test.
Based on numerous comprehensive specifications
automation suppliers will provide proven products and individual elements fully
documented to make up the required solution. Products and systems are enhanced
over time based on experience and the availability of new technologies.
Site integration
. Although apparently chaotic to the casual observer, the installation
and commissioning process is structured to ensure the complete testing of all
elements, making sure they work together successfully.
Operate and maintain.
As experience is gained of the process, procedures are
enhanced and the automation system finely tuned to ensure it meets operational
requirements. Safety‐related systems are tested to ensure they are available and
protecting the process from unwanted excursions and potential hazards.
Modify and enhance.
Over time, numerous modifications and enhancement will take
place. These will often draw on the specific skills offered by third party suppliers to
ensure that the right competencies are in place.
Individuals, departments and organisations work together, each contributing to
the overall safety of the process based on its scope of work and speciality.
Primary cause of failure
Most people in industry are familiar with the study carried out by the health and
safety executive called ‘Out of Control’. It investigated incidents caused by the
failure of protection systems in order to establish the primary cause and if there
was a pattern. Although the number of incidents studied is not statistically
significant, a clear pattern emerged. Failures were attributed to different phases
in the life of the process and it was noted that approximately 44% of failures
were attributed to the specification phase and a further 21% occurred during
design and implementation, installation and commissioning. That means 65%
of the total contributors to eventual system failure were already in place before
the system reached the operational phase.
Where process industries fail
So it was clear that each phase of the process life was responsible for either
creating errors or was responsible for not finding those from a previous phase
and therefore replicating them. The actual reasons for failure on numerous and
complex some possible contributors include the following.
Process design.
The process design phase including hazard and risk studies can vary
significantly both in the complexity and novelty in design. It leads to the generation of
numerous primary documents including the P&IDs. These prescribe what
measurement and control devices will be connected to the various parts of the
automation system. The connection between hazard and SIF starts to get lost