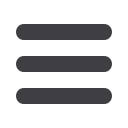

416
www.grovegear.comQuadro Accessories
Lecentric Helical-Aluminum
Lecentric Helical-Cast Iron
Technical Information
Mechanical Warnings
and Cautions
Terms and Conditions
SPEED REDUCER NOMENCLATURE & DEFINITIONS
BACKLASH
– Rotational movement of the output shaft when holding the input
shaft stationary and rotating the output alternately clockwise and counter clockwise.
Backlash is defined as the clearance between adjacent tooth flanks in a pair of
mounted gears. In any gearset, some amount of backlash (clearance) is necessary
to prevent damage brought about by gear tooth interference. Lack of backlash may
cause noise, overloading, overheating of gears and bearings and even seizing and
failure.
CENTER DISTANCE
– On a single reduction reducer, this is the distance between the
center lines of the input and output shafts. Shaft center lines may be parallel or at right
angles to one another. The center distance of multiple stage reducers usually refers to
the lowest speed stage (last reduction).
THRUST LOAD
– Forces imposed on a shaft parallel to the shaft axis. It is often
encountered on shafts driving mixers, fans, blowers and similar machines. When
thrust load acts on a speed reducer, you must be sure that the thrust load rating of the
reducer is high enough that it’s shafts and bearings can absorb the load.
MECHANICAL RATING
– The maximum power or torque that a speed reducer can
transmit, based on the strength and durability of its components, is it’s mechanical
rating. Obviously, the reducer may be rated no higher than the strength or durability
of its weakest component. Reducers typically have a safety margin of two to three
on their mechanical ratings. Thus, a reducer can withstand momentary overloads of
200-300% of its mechanical rating during a start up or other brief overload situations.
MOUNTING POSITION
– The relationship of the input and output shafts relative to
the floor line.
HORSEPOWER
– A measure of the rate of doing work and equals the power required
to lift 33,000 pounds one foot in one minute.
INPUT HORSEPOWER
– The amount of power applied to the input shaft of a
reducer by the prime mover is it’s input horsepower. It is often used as a selection
basis for power transmission components, and it appears in the rating table of drive
manufacturer’s published data. Remember that input horsepower ratings represent
the maximum amount of power that the reducer can safely handle.
OUTPUT HORSEPOWER
– The amount of power available at the output shaft of
a reducer is it’s output horsepower. Due to losses caused by inefficiency, output
horsepower is always less than input horsepower.
TORQUE
– A twisting effort tending to cause rotation. Because most power
transmission is associated with rotating elements, torque becomes important as a
measurement of the effort required to produce work in the rotational mode. Torque
is expressed as a force multiplied by a lever arm. It is stated in several units – pound
feet, pound inches, ounce inches, ounce feet, etc. However, the most commonly used
is pound inches.
In the case of speed reducers and gears, force or load is usually expressed in pounds
and distance in inches. For example, if a load of 10 pounds is applied to a shaft by
means of a wrench 9 inches long, we then have a torque of 10 pounds x 9 inches or
90 lb. in.
It is important to note that torque measurement is not dependent on time. The same
amount of torque may be required to run a shaft slowly or rapidly, but the introduction
of a time element causes work to be performed, and work is measured in terms of
horsepower. Consider the application of drawing water from a well via winch and
bucket.
In raising a 50-pound pail of water with a 10-inch diameter (5-inch radius) drum and a
10-inch crank arm, 25 pounds (neglecting friction) must be applied to the 10-inch crank
arm to overcome the torque created by the weight of the pail of water acting on the
5-inch drum radius. If no motion is involved, the system is in balance, and although
torque is being exerted, no work is being done. If the crank is turned at the rate of 10
RPM, the resulting work done is:
HP = T x RPM =
250 x 10 =
approx .04 HP
63,000
63,000
If the crank is turned twice as fast, the horsepower expended becomes:
250 x 20 =
approx .08 HP
63,000
Therefore, exerting the same torque at twice the speed requires twice the horsepower.
RATIO
– is defined as the driving speed divided by the driven speed. If a 1750 RPM
electric motor is used to drive a 350 RPM conveyor, the ratio would be a q750/350 =
5:1. Ratio is useful for calculating speed reduction and torque multiplication from driver
to driven member. For example, a 5:1 ratio Uniline speed reducer directly connected
to an electric motor would reduce the motor speed to 1/5 of its original value while
multiplying the motor torque to 5 times the original value (neglecting friction loses).
SPEED REDUCER SELECTION
– Before a reducer can be selected for any given
application, the equivalent horsepower is computed by multiplying the specified or
actual horsepower by the service factor for the particular load classification for which
the unit is to be used. It is necessary that the unit selected have a capacity equal to
or in excess of this equivalent horsepower. The recommended service factors for
various load classifications and duration of service are shown for several types of
prime movers on page 418.
Load classifications for various applications are given on page 418. They are
classified into three commonly recognized load classifications: Uniform, Moderate
Shock, and Heavy Shock.
Service factors represent the normal relationship between gear design power rating
and the continuous power requirements. Applications involving unusual or severe
loading or requiring a high degree of dependability should be carefully reviewed with
the manufacturer before a service factor is applied.
Applications with high-torque motors and motors for intermittent operations,
applications where extreme repetitive shock occurs, or where high-energy loads must
be absorbed, as when stalling, require special consideration and are not covered by
the service factors given on page 418.
When drives are equipped with brakes on the input, and the torque rating of the brake
exceeds the rating of the motor, the rating of the brake dictates the selection of the
gear unit.
The maximum momentary or starting load must not exceed 300 percent of rated load
(200 percent overload). Rated load is defined as the unit rating with a service factor
of 1.0.
Technical Information