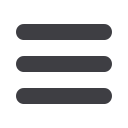

SPARKS
ELECTRICAL NEWS
SEPTEMBER 2016
11
Please contact your nearest sales office for further details. www.zestweg.com Tel: +27 11 723 6000 Extended Guarantees on WEG ProductsZestWeg_463_ext_Sparks_285x50.indd 1
2016/01/27 8:26 AM
CONTRACTORS’
CORNER
SHOWCASING SOLUTIONS
AND SUPPORT SYSTEMS
OFFERING COMPLETE CONFIDENCE,
CERTAINTY AND COMFORT
I
T is never just about supplying products or tech-
nical support to the market. It is also about im-
plementing best practice across all companies
and in particular manufacturing operations.
Louis Meiring, chief executive officer of the Zest
WEG Group, says that it is this operating philosophy
that has seen the Group’s holding company, WEG
Brazil, continue to invest in the local operation’s
manufacturing facilities. Significantly, Zest WEG
Group will be exhibiting its locally manufactured
custom equipment at Electra Mining Africa 2016.
Meiring says that the most recent investment
has been in best practice production control pro-
grammes that will allow the Zest WEG Group
manufacturing operations to improve processes
thereby accelerating production and meeting the
shortened lead times which have become the
norm in the market.
He explains that decision to introduce WEG’s
manufacturing planning and execution system into
the South African operations forms part of the glob-
al sustainability strategy. “It was always the intention
to implement best practices at these facilities with
the long term objective of enabling these manufac-
turing plants to produce product for the internation-
al market,” he says. Eventually, WEG will be able to
manufacture at any of its centres worldwide.
“Zest WEG Group as an organisation is very ex-
cited about this step and particularly the very clear
benefits that our customers will see,” Meiring says.
“It will make a massive contribution to the success
of our local manufacturing facilities and put us into
the international space.”
Juliano Vargas, Zest WEG Group logistics and
operations director, explains that the manufacturing
planning and execution system being used is well
proven at other WEG manufacturing facilities.
“The system facilitates full control of all our man-
ufacturing operations, and importantly provides ac-
curate cost and time control. Access to this level of
information allows a high degree of certainty and
creates an environment where customers can have
complete confidence and comfort,” Vargas says.
“Continuous improvement programmes have en-
sured that the system functions optimally and what
is most important is that the system implemented
at the South African manufacturing operations has
been localised,” he explains. “This means that South
Africa was able to draw on the experience of all
WEG facilities with the result that the system con-
siders the exact Zest WEG Group operational condi-
tions while still achieving best practice criteria.”
Zest WEG Group currently operates four separate
manufacturing facilities being Shaw Controls, WEG
Transformers Africa Wadeville, WEG Transformers
Africa Heidelberg and Zest WEG Group Generator
Sets Division.
Vargas says the system will enable greater and
transparent communication with customers in
terms of the status of each order. “Access to in-
formation is in real time and is so specific that at
any point in time a customer can find out the exact
stage at which the product is during the manufac-
ture process,” he says.
This is most significant especially given the dy-
namic nature of business at the moment where
manufacturing facilities often receive change no-
tices or order amendments even once the produc-
tion process has begun. Being dynamic, the system
allows for the simulation of the change to be done
and an accurate prediction made with respect to the
impact in cost, time and order conclusion.
Commenting on the actual implementation, Var-
gas says that the planning stages started mid-2015
when the alignment between the Zest WEG Group
and the WEG teams was made.
In November 2015, a team of skilled practitioners
from WEG Brazil visited the South African facilities
to assess these operations and establish the status
compared to WEG global best practices in manu-
facturing. This took place over a three week period
to ensure in-depth assessment of all four facilities.
Comparisons were done with WEG facilities in
Colombia, Brazil and Mexico. These operations
produce the same or similar products which meant
that the manufacturing processes are the same and
similar. These facilities already complied with WEG
best practices, and Vargas says that some had done
so for more than 20 years.
“The resultant gap analysis between the Zest
WEG Group status and that of WEG’s best practices
formed the foundation from which the implementa-
tion stage began,” Vargas says.
The gap assessment was discussed in depth with
WEG Brazil and the implementation plan was de-
veloped in conjunction with a local partner in South
Africa. The implementation phase started in March
this year and consisted of a couple of facets. A team
of practitioners from Brazil that had already im-
plemented similar systems at other WEG facilities
joined the local team, and the system went live mid-
June with the support of the full team.
Vargas pays tribute to the implementation team
and all at the Zest WEG Group manufacturing op-
erations as he underscores the fact that on day one
of going live it was possible for all facilities to oper-
ate normally.
“We cannot say it was effortless, but we can say
that the implementation was thorough and custom-
ers have already started realising the benefits of the
significant investment WEG has made in the four
manufacturing operations,” Vargas says.
Meiring concludes by confirming that being re-
sponsive to the market has always been the corner-
stone of Zest WEG Group’s success on the African
continent. “It is this ability to adapt our business that
we believe will enable us to become the supplier of
choice to the market.”
Enquiries: +27 11 723 6000
VERT
Energy is participating at the Powerex show at Electra Mining, to
be held at Nasrec from 12 – 16 September 2016 (Stand B06, Hall 9).
“As a service provider to the diesel, gas, wind and hydro generator set
building industry, we believe this show will be the perfect forum for Vert
Energy to display and demonstrate our solutions and support service
to key players in the electric power generation and electro-mechanical
sectors,” says Vert Energy’s managing director, Grant Robertson.
“Escalating energy requirements have placed power utilities under
enormous pressure throughout the African continent, which is why
companies are investing in alternative sources of electricity production.
“Through an extensive range of quality branded EPG products and
a highly skilled team of technical experts, Vert Energy plays a major
role in providing dependable power to companies, even in the most
remote regions.
“As part of our commitment to the genset manufacturing sector,
for the swift supply of reliable components, the company has made
a substantial investment in sourcing the finest components that pro-
duce electric energy from mechanical energy and which withstand
harsh operating conditions.”
Vert Energy has been appointed distributors in sub-Saharan Africa
for leading brands, which are supported by original spare parts and
accessories. These components include Leroy Somer alternators;
a wide range of electric motors and drives; DEIF controllers; ASCO
automatic transfer switches; API Covrad radiators and Avtron and
Froment load banks, as well as customised control panels.
Vert Energy is the exclusive distributor of Leroy Somer LS alterna-
tors, the largest producer of alternators for gensets globally. These
alternators are available from 5 kVA to 20 mVA from 48 Vdc to
11 000 V. On display will be the new LS range of two-pole alterna-
tors for portable power, as well as variable speed alternators, designed
especially for the telecoms market.
Also on show will be DEIF power and control components, including
the new automatic sustainable controller (ASC). This is the first fully
integrated control solution between renewable energy inverters and
traditional diesel generators.
Vert Energy will also be showcasing the ASCO Series 230 automatic
transfer switch, which consists of an intelligent controller and a modular
load break switch that automatically transfers the load to the emer-
gency power source when it detects under and over voltage, under and
over frequency, or phase failure.
Avtron and Froment power test solutions are used effectively for the
exercise and verification of diesel gensets, gas turbines, UPS systems,
wind and solar, as well as agricultural tractors and self-propelled ma-
chinery. Covrad’s turnkey radiator cooling packages feature high-per-
formance cores and low horsepower fans, engineered into a compact
envelope to deliver maximum cooling, in the smallest footprint.
A critical part of Vert Energy’s service is the availability throughout
Africa of factory and OEM trained technicians who cope efficiently with
any electro-mechanical breakdown situation or routine preventative
maintenance procedures.
Enquiries: +27 11 453 9669
Zest WEG Group’s panel manu-
facturing facility in Cape Town.