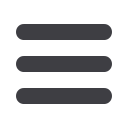

44
Tube Products International January 2010
www.read-tpi.comFi t t ings
Parker Hannifin’s new production process is based on stainless steel extrusions
S
S
A-Lok compression tube fittings
mechanical properties, and are in fact
stronger than traditional forged parts.”
Parker Hannifin believes it is the first
tube fittings manufacturer to launch
extrusion-based products into the
mainstream twin-ferrule stainless steel
compression tube fitting market, and
is offering the technology on its A-Lok
range.
It has been able to make this move
thanks to a patented extrusion process
that can cope with the tough metals
required for tube fittings. Parker also
notes that the process is equally
applicable to all the exotic alloy fitting
products it supplies for corrosion-
resistant applications.
As extrusions allow dimensions to
be very closely controlled, the fitting
interchangeability demanded by large-
scale users remains in place. Switching
Parker Hannifin’s instrumentation
products division has introduced a new
production process based on stainless
steel extrusions, to raise the quality
and consistency of industry-standard
compression tube fittings.
The technology is aimed at users in
processing markets such as oil, gas and
chemicals, where the need for integrity
and reliability is paramount.
“By complementing our traditional
forged fittings range with versions
made from extruded materials, we have
been able to increase the quality and
consistency of finished parts without
raising costs,” commented Sheldon
Banks of Parker Hannifin.
“The exceptional uniformity of metal
grain size and shape inside extrusion-
based parts means that all the new
fittings possess virtually identical
to extrusion-based fittings can bring
further benefits for end users, especially
those working on projects. Extruded
profiles are faster to produce and are
available with shorter lead times, and
can typically be produced in smaller
batches. This allows Parker to respond
more quickly and flexibly to customer
requests, which can be beneficial for
projects requiring exotic materials.
Parker has a policy of sourcing raw
materials from high quality European
sources, and this is complemented by
independent intergranular corrosion
testing before product manufacturing
begins, plus a number of unique
processing stages aimed at optimising
reliability and corrosion resistance.
Parker Instrumentation Products
Division
– UK
ipd@parker.com www.parker.com