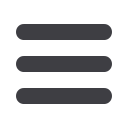

LS6 28” extended length stacker. “This configuration gives us a
lot of versatility,” DeBoer comments. “The extended length
stacker enables us to produce a six-pager for more versatility in
format, but the DP6 Dynamic
Perforator is the star of the line.
Imagine a mailer sending
coupons. I’m a new customer, I
just moved into the area, and I
receive two coupons, while my
next-door neighbor, who has
lived there a while, only receives one. Because I can dynamically
perf in-line, I can produce these two very different pieces in the
same run, allowing us to optimize postal sorting and save the
customer on postage costs. I’m not familiar with any other
system that will do that in-line.” The entire solution goes from
white paper roll to fully-separated printed stacks with full-bleed
and variable perforations from sheet to sheet, with no manual
touchpoints.
DeBoer points out that the company had a concern with putting
all of this in-line. “The presses run all the time,” he says, ”and we
were worried that downtime on the finishing line would cause
a bottleneck for us. These things just run. Standard doesn’t sell
the least expensive solution in the market, but you get the
value you pay for. I don’t see their technicians in here all the
time, and that is a good thing!”
Capitalizing on the Benefits of Web-Fed
Printing
The success of that first in-line finishing solution led Darwill to
equip its second Canon ColorStream press with a Hunkeler Roll-
to-Stack solution as well. With two production inkjet presses
now in house, Darwill took the next logical step: installing a
web-fed inserter in its bindery. “We just installed a Hunkeler
RW6 Rewinder on our Canon ColorStream 3900, which gives
that line the capability to go roll-to-roll,” DeBoer states.
“Especially for those longer runs, which our sales force has
been so successful at selling, we can now more easily do jobs
that use a full roll, or even multiple rolls, and move them right
over to our roll-fed inserter. And also having the roll-to-stack
capability on the 3900 gives us the ultimate in flexibility.”
Book It
With these two highly versatile Hunkeler configurations, Darwill
is also able to efficiently produce booklets, especially with the
help of their Horizon equipment, secured through local
Standard dealer Accurate Printing Repair and Sales in Lombard,
Illinois. “We have a Standard Horizon StitchLiner 5500 Saddle-
stitcher with sheet feeding for digitally collated sets, and two
Standard Horizon CRF-362 Creaser/Folders. We use those in
conjunction with both our digital sheet-fed HP Indigos and
Xerox iGens as well as with our roll-fed production inkjet
presses. That allows us to take a stacked, collated set from any
of our presses through to finished customized booklets in a
very efficient manner.”
Working with Standard
“We have a terrific working partnership with Standard,” DeBoer
says. “They helped us through the transition into working with
a roll-fed workflow, and they have taken the time to
thoroughly understand our business and where we are going
with it, and to help us achieve our goals. That makes it easy for
us to work with them on an ongoing basis to create the best
solutions to meet our customers’ existing and emerging needs.
Their name recognition and the quality of their products, along
with this spirit of true partnership, is why we keep coming
back to them. It’s a huge feather in their cap!”
Darwill, now based in Hillside, Illinois, was founded more than
a half-century ago as a family business, with the founder
selling during the day and printing at night. Over the ensuing
years, the company continued to grow and innovate, getting
into variable data printing more than 20 years ago, producing
highly customized benefits statements.
But the truly transformational move came when Darwill
acquired a Canon ColorStream 3500 continuous-feed
production inkjet press. “We knew we had a certain amount of
volume that we could transition to a white-paper-in model,”
says Mark DeBoer, the company’s Director of Customer
Experience. “That was where we could reduce waste and
inventory for our clients, and where color matching was not as
critical since everything would be printed in one pass. This
shaped our investment decision, and that has led to waves of
transformation ever since.”
DeBoer points out that Darwill had always been a sheet-fed
operation. “There was a lot to learn adding roll-fed to the mix,”
he adds. “That includes storing and moving large rolls of paper,
which we didn’t have to deal with before.”
Darwill has a good mix of both long-run and highly customized
short-run work. “It wasn’t too much longer before we added a
second roll-fed press, a Canon ColorStream 3900,” DeBoer says.
“The 3900 was both a back-up
system and for use in longer runs
that are now becoming more
common in our business. A key
configuration consideration for
both systems was the finishing.”
Market Differentiation
Darwill collaborated with Standard Finishing Systems and
Canon to design an in-line finishing solution for its first
production inkjet press. “We wanted efficiency, of course, but
we also wanted some unique capabilities that could help us –
and our customers – differentiate ourselves.”
Darwill chose to add a roll-to-stack solution and dynamic
perfing capability to its Canon ColorStream 3500. The Hunkeler
Roll-to-Stack line includes a DP6 Dynamic Perforator and an
Maria Velasco operates the Standard Horizon StitchLiner 5500
Saddlestitcher with sheet feeding for digitally collated sets, while Ron
Trydal works with one of two Standard Horizon CRF-362 Creaser/ Folders.
These systems allow Darwill to take a stacked, collated set from any
press through to finished booklets in a very efficient manner.
Finish
Line
11.2016
Finish
Line
11.2016
4
With a good mix of long-run and highly customized short-run work, in-line finishing makes an impact.
Darwill: Leveraging Dynamic
Finishing to Stay Ahead of the Pack.
Transitioning from a sheet-fed to roll-fed workflow.
5
The Hunkeler Roll-to-Stack line includes a DP6 Dynamic
Perforator and an LS6 28” extended length stacker. The entire
solution goes from white paper roll to fully-separated printed
stacks with full-bleed and variable perforations from sheet to
sheet, with no manual touchpoints.
Hunkeler Roll-to-Stack with Dynamic Perf
Customer Profile
I
Standard has taken the time to
thoroughly understand our business
and where we are going with it, and
to help us achieve our goals.
Darwill recently added a Hunkeler RW6 Rewinder to its second Roll-to-Stack line,
which now has the capability to also go roll-to-roll.
Bob VanWinkle operates the Canon ColorStream press with in-line Hunkeler
Roll-to-Stack solution and DP6 Dynamic Perforator.
Brandon Van Dyke, Co-CEO and Mark DeBoer, Director of Customer Experience
stand in front of the Standard Hunkeler Roll-to-Stack solution at Darwill.