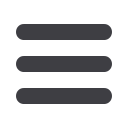

31
Chemical Technology • August 2015
Types of vaporisers
Typical types of vaporisers that have been used worldwide
for LNG regasification are:
• Open Rack Vaporisers (ORV)
• Submerged Combustion Vaporisers (SCV)
• Ambient Air Vaporisers (AAV)
• Intermediate Fluid Vaporisers (IFV)
Open rack vaporisers (ORV) and submerged combus-
tion vaporisers (SCV) are the most common vaporisation
methods in existing regasification terminals, which have
generally been located in the subequatorial region. Recent
LNG receiving terminal activities have been shifting to the
equatorial region where the weather is warmer, and the use
of intermediate fluid vaporisers (IFV) is found to be more
suitable. Important factors that should be considered in the
LNG vaporiser selection process are:
• Site conditions and plant location
• Availability and reliability of the heat source
• Customer demand fluctuation
• Emission permit limits
• Regulatory restrictions with respect to the use of seawater
• Vaporiser capacity and operating parameters
• Safety in design
• Operating flexibility and reliability
• Capital and operating costs.
Seawater (SW) heating
LNG receiving terminals are generally located close to the
open sea for ease of access to LNG carriers. Seawater is
generally available in large quantities at low cost as com-
pared to other sources of heat, and is the preferred heat
source. The oppositions are concerns about the destruction
of marine life within the seawater system and the negative
impacts from the cold seawater discharge and the spent
chemical disposal.
Open rack vaporiser (ORV)
An Open Rack Vaporiser (ORV) is a heat exchanger that
uses seawater as the source of heat. ORVs are well proven
technology and have been widely used in Japan, Korea and
European LNG terminals. The common seawater tempera-
ture for ORV operation is at least 5 °C.
ORV units are generally constructed of aluminumalloy for
mechanical strength designed to operate at the cryogenic
temperature. The aluminum material has high thermal
conductivity which is important for heat transfer equipment.
The tubes are arranged in panels, connected through the
LNG inlet and the regasified product outlet piping manifolds
and hung from a rack (Figure 1). The panels are coated ex-
ternally with zinc alloy, providing corrosion protection against
seawater. The panel arrangement feature provides ease of
access for maintenance. ORVs require regular maintenance
to keep the finned tube surface clean.
The ORV design is very flexible. The panels can be iso-
lated for maintenance and heating duty can be adjusted
as needed. The unit can be turned down to accommodate
fluctuations in gas demand, gas delivery temperature and
variation in seawater temperature.
For large regasification terminals, detailed evaluation of
the seawater system including future expansion must be
DESIGN AND MATERIALS OF
CONSTRUCTION