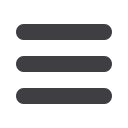

CAPITAL EQUIPMENT NEWS
AUGUST 2016
8
CAT
®
816K LANDFILL COMPACTOR
designed for optimum compaction performance
T
he new Cat
®
816K landfill compactor
builds on the established performance,
durability, and reliability that the model
816 has demonstrated since 1972. The new
K Series model, designed with heavy-du-
ty main structures that support multiple life
cycles, features a fuel-efficient Cat C7.1
ACERT™ engine, single-lever steering, pres-
surised cab, and wheel/tip options that provide
extended service life. Available Cat COMPACT
Technologies, such as Compaction Control,
further enhance compaction performance and
consistency by providing accurate compaction
values and 3D mapping.
Structures/guarding/wheels/tips
The foundation of the 816K’s purpose-built
design is its massive, robotically welded
main structures, featuring a full box-section
rear frame that resists torsional shock and
twisting forces, heavy-duty steering cylinder
mounts to efficiently transmit steering loads
into the frame, and an axle-mounting design
that is optimised for increased structural
integrity.
Three new wheel and tip configurations allow
matching the 816K to the application. The
Paddle Tip reduces weight and provides high
performance with reduced fuel burn. The Plus
Tip provides increased side-slope stability,
and the Combination Tip provides an effective
compromise of performance, fuel economy,
and side-slope stability.
In addition, specialised guarding protects
components from damage, debris accumu-
lation, chemicals, and premature wear, in-
cluding axle guarding that prevents material
from wrapping and binding around the axles.
The transmission oil tube is guarded, and the
fuel tank is positioned away from debris in the
front frame. A screened air inlet for the radia-
tor is placed high at the rear of the machine to
prevent debris from blocking airflow, and the
grille’s design allows trash to fall away. Striker
bars are designed to keep wheels free of de-
bris, and optional cleaner fingers are available
for use in cohesive soils and in material that
packs between tips.
Power train
The C7.1 ACERT engine meets U.S. EPA Tier
4 Final/EU Stage IV emissions standards
with advanced technologies that do not
interrupt the machine’s work cycle. (A Tier
3/Stage IIIA equivalent configuration is
available in certain areas.) The Cat Next
Generation high-pressure/common-rail fuel
system delivers fuel in a precise series of
micro-bursts during each cycle, providing
extremely efficient combustion, and control
systems lower the engine’s average working
speed for reduced heat loads and added fuel
efficiency. An engine-idle-shutdown system
saves fuel by eliminating excess idling.
The 816K’s Caterpillar built planetary pow-
er-shift transmission features special met-
allurgy and gear heat-treating to ensure
long term durability. The transmission’s Ad-
vanced Productivity Electronic Control System
(APECS) is designed to improve transmission
shifting performance, provide a higher level
of operator comfort, and increase production.
Heavy-duty planetary axles complete the pow-
er train, the front is fixed and the rear oscil-
lates ± 6 degrees.
Operator’s environment
The 816K’s Cat STIC™ Steering and
Transmission Integrated Control combines
steering and transmission control (directional
and gear selection) into a single lever. Simple
side-to-side movements of the low-effort
lever provide precise steering manoeuvres
through 42 degrees of articulation right and
left. Electro-hydraulic implement controls use
soft detents, and cylinders use electronically
controlled stops for smooth operation. The
left pedal serves as a brake, transmission
neutraliser, and decelerator that overrides the
engine-speed setting.
The operator’s environment is kept clean
via filtered air that pressurises the cab, and
temperature is maintained with an auto-
matic climate-control system. The cab is
isolation-mounted to reduce vibration, and
operator comfort is enhanced with an air-sus-
pension seat or the available Cat Comfort Se-
ries III seat. Back-lighted membrane switches
have LED indicators and ISO identification,
and a standard rear view camera system en-
hances operator awareness.
Serviceability and sustainability
Routine service points for the 816K,
including grease fittings, are grouped for
convenience and reached from ground
level via swing-out doors or from non-slip
platforms. A ground-level service panel
includes a master disconnect switch with
integrated lock-out/tag-out, DEF purge
lamp for Tier 4 Final/Stage IV machines,
circuit breakers, fuel-shutoff switch, and
jump-start receptacle. Ecology drains help
prevent spills, and side doors facilitate
cleaning of the cooling system.
The 816K is designed for multiple machine
lives and component rebuilds utilising Cater-
pillar’s sustainable options such as the Reman
and Certified Rebuild programmes. These op-
tions could save a customer up to 70% of
purchasing a new comparable machine by
reusing components or replacing with man-
ufactured components.
Cat Connect Technology
The Cat Vital Information Management sys-
tem (VIMS™) notifies operators and tech-
nicians about potential problems, allowing
issues to be resolved quickly, preventing
unscheduled downtime. In addition, Cat
LINK technologies wirelessly provide equip-
ment managers with critical information, via
the VisionLink
®
interface, including ma-
chine location, hours, fuel usage, idle time
and event codes.
Cat COMPACT technologies combine ad-
vanced compaction measurement, in-cab
guidance, and reporting capabilities to help
consistently meet compaction targets, uni-
formly, in fewer passes, saving rework time
and fuel. The factory-installed Cat Compaction
Control system measures compaction values
and provides 3D pass-mapping guidance that
indicates when layers have reached optimum
density. Mapping helps eliminate voids, opti-
mises cell space, and documents results.
b