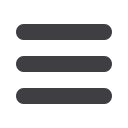

CAPITAL EQUIPMENT NEWS
AUGUST 2016
16
Oscillation
During oscillation, the drum is equipped with two eccentric
imbalance shafts rotating in sync. The imbalanced weights on the
two shafts are arranged opposite each other and force the drum to
rotate rapidly, alternating in a forwards-backwards movement. In
contrast to the vibrating drum, the oscillating drum does not lose
contact with the surface and in effect ‘massages’ the material to
achieve compaction.
During oscillation compaction, both the forward and backward ro-
tating movements of the roller drum transmit shearing forces into
the soil or asphalt. This ‘double frequency’ and permanent contact
of the rollers’ own static weight causes the material to compact
more quickly. On the other hand, the vibration drum executes an up
and down movement and each time the imbalance weight rotates,
it transmits a vertical force to the material along with the static
weight of the machine one vibration at a time.
As with vibration, the compaction performance of the oscillation is
based on well matched amplitudes and frequency. However, an ad-
vantage of the oscillation technology is its self-regulating amplitude
which is regulated by the material that is being compacted. This
means that as compaction causes the material to become more
rigid, the amplitude decreases automatically and over-compaction
is avoided.
Compaction has evolved from the 1800s when rollers were made
of stone or cast iron and drawn by man or beast during construc-
tion. Today, we are faced with physical, environmental, human
and statutory challenges during construction work. Therefore
having the right equipment and choice of technology is important.
Of even greater importance is knowing when and how to apply
this technology.
b
I
n its previous column (CEN May 2016) Wirtgen discussed
Compaction Methods namely, Static and Dynamic. It further noted
that Dynamic Compaction could be divided into Vibration and
Oscillation.
What then is oscillation, introduced by Hamm in 1983, and what are
the benefits?
Vibration
During compaction, the vibration of the roller drum is generated
by the rotating imbalance weight whose rotation speed determines
the vibration frequency. The imbalance weight consists of a fixed
part and a moveable weight. The position of the moveable weight
depends on the direction of rotation of the exciter shaft. The effective
weight of the imbalance weight increases or decreases depending on
the direction of rotation. This allows the roller drum to vibrate at two
different amplitudes.
Operator & Machines
Compaction
Soil Compaction
Asphalt Compaction
Surrounds and Environment
Less vibratory impact provides
better driver comfort
High compaction through
combination of static and
horizontally applied shear forces
No particle destruction due to
high impact forces
Effective compaction at lower
temperatures
Lower impact level so less effect on already
compacted surfaces in adjacent areas
Lower noise levels
Constant contact with the
surface, load and shear forces
are continually applied to
achieve density quicker
Good surface compaction and
avoidance of unravelling from
over compaction
Good surface sealing and finish Lower impact and noise levels so less effect
on surrounding buildings, underground
services and inner city neighbourhoods
Fewer resonances so less
stress on the machine
structure
Fewer passes means lower fuel
consumption
Good course bonding
No particle destruction on existing
material during hot-on-cold seam
compaction
Risk-free compaction in multi-story carparks
or on concrete structures
THE BASICS OF SOIL COMPACTION –
Oscillation
Oscillating technology has an effect on the operator, machine, compaction and the surrounds: