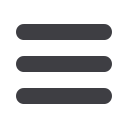

CAPITAL EQUIPMENT NEWS
MAY 2016
22
WORK @ HEIGHT:
FROM THE BOARD
WORLD NEWS
LAUNCH OF GUIDELINES FOR SAFE WORKING AT HEIGHT – 10 OCTOBER 2016 AT BYTES
CONFERENCE CENTRE, MIDRAND
As indicated before, the IWH and relevant
stakeholders from the industry, embarked on the
development of a set of Guidelines for Safe Working
at Height. This document will be made available
for the benefit of anyone supervising, managing
or carrying out tasks in any place considered to
be working at height. The Guidelines have also
received the official approval of the Department of
Labour, through Mr Tibor Szana’s office.
South African National Standards, SANS, are those
most used within this document and the industry at
large. Alternatives, such as International Standards,
have also been considered to be 'Good Practice' if
their requirements are above those of SANS Codes
and/or no SANS code exist for that item.
The Guidelines will officially be launched on the
10 October 2016, at Bytes Conference Centre in Mid-
rand where the Chief Inspector, Mr Tibor Szana will
deliver the Keynote Speech.
The purpose of the guidelines document is to pro-
vide people with the necessary basic knowledge to un-
derstand and make safe any task that is to be carried
out at height. It was developed with input from several
industries 'experts', in their individual fields, looking at
ways of improving current practices and making work
at height safer for everyone.
The scope was not to focus on any one particular
industry, such as construction or mining, but rather at
anybody who “through the course of their work was
required to be in an elevated position and have a risk
of falling”.
Falling from height, or being struck by objects that
fall from height, results in more death and disabling
injuries than any other occupational cause. This is not
only in South Africa but across the world in developing
and advanced nations. Therefore, developing the fun-
damental duties of employers will only work to reduce
the number of fatalities and disabilities caused in this
way.
The duties can be broken down as
follows:
• Developing and implementing safe systems of
work.
• Providing safe access and egress to work locations.
• Confirming work locations are safe and remain that
way throughout every task.
• Ensuring safe equipment is provided, maintained
and used correctly.
• Confirming employees are competent to do the
work expected of them.
We hope that readers will be able to see that we
have tried to provide suitable and sufficient content to
allow informed decisions to be made whilst applying
those duties of care. Taking a step back, before
work commences, to ask “have we done enough
to safeguard ourselves and others?” is paramount
to successfully working safely at height. This, and
carrying out any activity in a safe and controlled
manner.
Although we have tried to cover every angle, unsafe
acts and conditions may still lead to events that cause
injury or ill health to workers and people affected by
tasks being carried out. This is why accidents, near-
miss events and dangerous occurrences must form
part of the overall planning of safe work at height. All
companies must have a policy and procedure in place
for reporting such events and should always follow the
stated protocols and reporting methods, ensuring the
employer is notified immediately. In addition, the acci-
dent scene should never be tampered with, unless to
save life or prevent further harm, until authorised to do
so by the employer.
Rescue must also be an integral part of the pol-
icy and procedures. Looking at the probabilities of
how harm will occur will provide the best insight into
necessary equipment and methods required for po-
tential rescues. Carrying out training and drills, with
the people involved with rescue teams, will further
assist in achieving the ultimate goals. The ultimate
goals are to prevent accidents, save life and reduce
the numbers of working at height events that cause
the death, disabling injuries and suffering that poor
planning encourages.
With organisations/bodies such as Department of
Labour, IOSM, SAIOSH, MBA being involved in the
development of the document and endorsing it, these
guidelines will assist greatly not just in advising the
industry at large but also being accepted by people
involved in working at height.
Interested people who would like to attend the
launch on 10 October or buying the guidelines
document is welcome to contact us via email at
pa@profbody.co.za.
b
Dr ALTI KRIEL, CEO: IWH
JCB UPGRADES
TELEHANDLER
JCB has debuted in the North
American market with a new tele-
handler, the 540-140 HiViz which of-
fers a 4 000 kg maximum lift capaci-
ty with a maximum lift height of 22 m
on wheels and 26 m on stabilisers.
The 540-140 HiViz Loadall has the
lowest boom mounting in its class,
up to 24 cm lower than the stan-
dard 540-140. The boom section has
been reduced by 34 cm to coincide
with the overall height advantage.
Hydraulic performance is closely
matched with the engine’s output,
while lift performance has been
tailored to the machine’s stability,
both when working on wheels and
with the stabilisers down.
MAGNI INTRODUCES FIXED
BOOM TELEHANDLER
Italian telescopic handler manufac-
turer, Magni TH, displayed its first
fixed boom telescopic handler at
BAUMA 2016 – the TH6.20, with a
maximum capacity of 6 tonnes and
a working height of 20 m.
The range will consist of three
models – 10, 15 and 20 m working
height.
The machines will have the same
pressurised and airtight full visi-
bility cabs of the RTH models with
standard heating, air conditioning
and 100 % inlet air filtration. The
cab will also be fitted with Magni’s
touch screen and MCTS system to
control the machine.
ERRATUM
We appologise for the error in the
last work@height newsletter where
Jean DuRandt was reffered to as the
CEO of Eazi Group. Jean DuRandt is
the GM GS of the Eazi Group