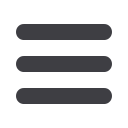
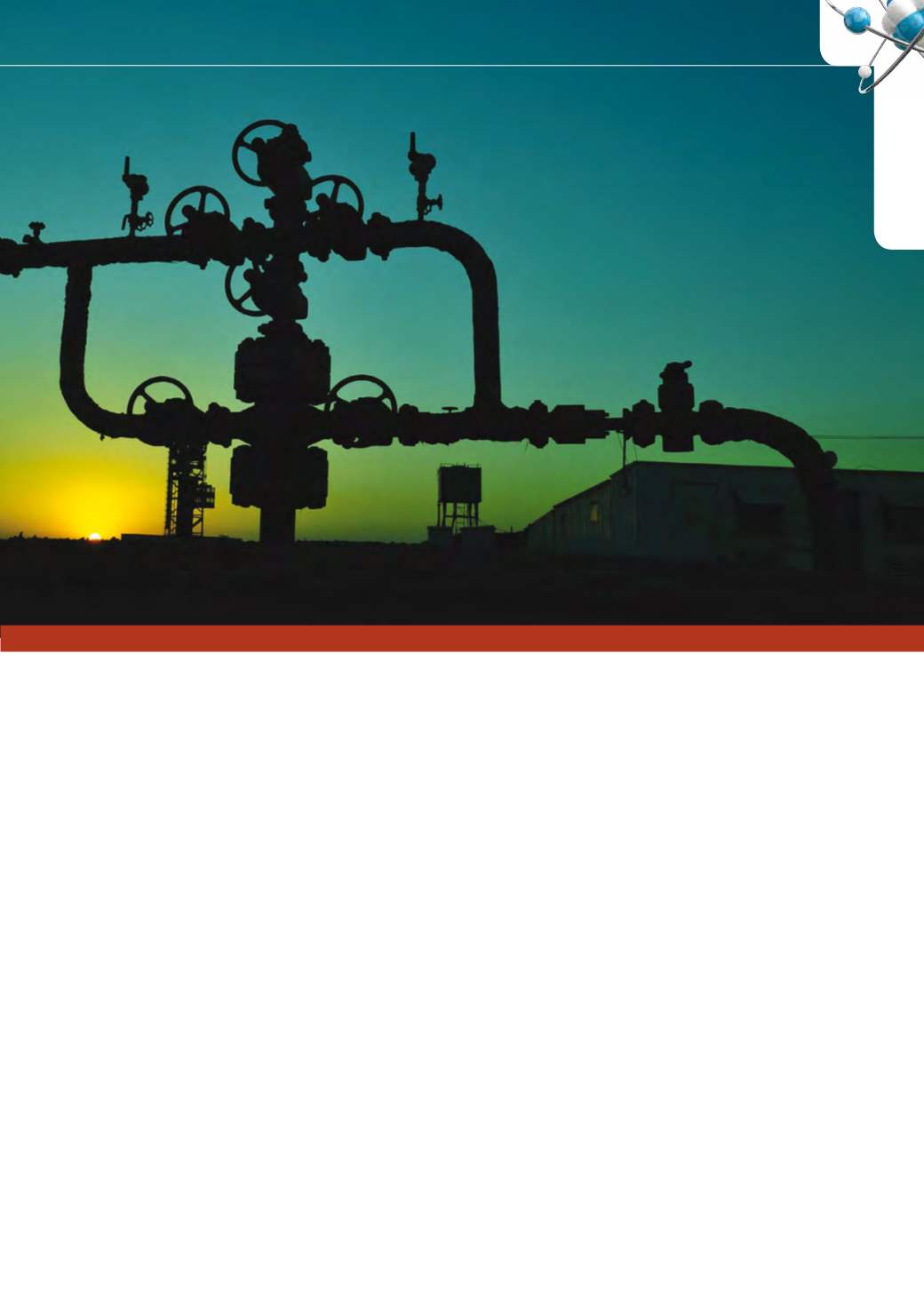
Chemical Technology • December 2015
9
PUMPS & VALVES
rule, the activities are the responsibility of the engineering
contractor.
Determining the requirements
In the typical design process for a new unit, after the feasibil-
ity studies as to the economics of the unit and the concep-
tual engineering has been done, the first set of drawings
to be produced are the metallurgical flow diagrams. These
drawings show most of the equipment and the major lines
connecting them, and are used to work out heat and mate-
rial balances and as aids in sizing the major equipment. The
only valves that are shown are the principal control valves,
and those are primarily shown to diagram the logic used
to control the process (flow into a particular column being
dependent on the temperature in the column, for instance).
After these drawings are approved, engineering proceeds
on the next set of drawings, where the majority of the valves
are displayed for the first time. These are known as the piping
and instrument diagrams (P&IDs), also known as process
flow diagrams and utility flow diagrams, depending on the
system they portray.
The flowsheets are used to help write piping line classes.
The line class groups related services together, to organise
the requirements for specific services as to corrosivity, wall
thickness and so on. This information, along with design
conditions, determines what material is required for valve
body and trim, and pressure rating and size range.
What a contractor needs frommanufacturers at the design
and selection stage is:
• Catalogue data (published on paper or online) showing
what is available, and what the product size ranges are,
including dimension tables;
• Drawings or descriptions showing how the valve operates
(for unusual or proprietary designs);
• Confidence that these valves really exist, and have been
built before.
Describing the valve
There are two types of valves used in plants, namely ‘tagged
items’ and ‘bulk items’.
Any valve that is sized specifically for the flow conditions
that exist in one location is assigned a tag number. One ex-
ample of this is a control valve, whose functioning depends
on process data taken from points nearby and whose output
is a process variable for the next piece of equipment in line.
This valve is a unique item whose tag number is assigned
based on a structured format which is easily identifiable by
process control systems (DCS or PLC, for example).
Other tagged items may include specially-sized valves
such as boiler blowdown, which are not connected to any
control systemand thusmay be numbered as specialty items
or minor equipment items. There are also automated on-off
valves, which are not control valves but are connected to a
control system and thus have an ‘address’ for the control
system to interface with.
These valves are described on a data sheet, one for each
valve, with its process data, actuation data, power source
data, and a brief description of the valve type and material.
These forms are now often automated, wherein the data
can be input and maintained in an electronic format, often