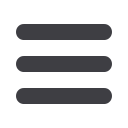

ABB Limited
Please reply to:
Tel: +44(0)1642 372000
Website:
www.abb.comRegistration no:
Registered Office:
Pavilion 9, Byland Way
3780764 England
Daresbury Park
Belasis Hall Business Park
Fax: +44(0)1642 372111
E-mail:
info@gb.abb.comDaresbury, Warrington
Billingham TS23 4EB
VAT Reg No:
Cheshire WA4 4BT
United Kingdom
668 1364 13
United Kingdom
The Silo factor - Why tackling silos can improve safety performance
and increase availability of your processes.
Karl Watson, Process Safety Product Manager, ABB OGC BU, Belasis Hall Technology Park, Billingham TS23 4EB
Abstract
The functional safety lifecycle involves an array of disciplines, functions, and often
businesses to ensure that hazards and associated safety systems are correctly assessed, specified,
designed, delivered and operated and maintained. Ensuring a sustained safety performance and
identifying opportunities to learn and improve, however, can only be achieved through integrated
thinking and processes to ensure that focus remains on Major Accident Hazards.
Amid tighter budgets and a sharper focus on balance sheets, however, safety performance is being
threatened by the interminable rise of the silo factor – an inability within functional safety circles to
collaborate and be consistent with other departments, which is negatively affecting safety
performance and is being exacerbated by the drive for cost reductions in many industry sectors.
Any person responsible for process and functional safety in an operating company needs to be able
to answer ‘yes’ to the following three questions:
•
Do we understand what can go wrong?
•
Do we know what systems we have to prevent this happening?
•
Do we have information to assure us these systems are working effectively?
This paper focusing on the issue of ‘silo working’ and shows how a collaborative approach can
result in ensuring you can confidently answer those 3 questions, deliver systems which have an
optimised cost of safety and can have a benefit of improving equipment availability, which results
in increased production.
Introduction
Efforts to galvanise global industries against the threat of hazardous catastrophes are being hampered
by an uncoordinated and disjointed approach to Process Safety Management (PSM) - the silo factor.
This is the principle finding of a research project carried out by ABB Consulting, based on almost 500
recommendations from 16 site process safety risk assessments carried out over recent years.
Here we present the common PSM weaknesses that have been identified, with respect to Functional
Safety Management, discussing their underlying causes and present some ideas on how to eradicate
the factors that can lead to silo thinking.
Without urgent attention to this endemic problem, we could be lowering our defences against more
disasters on the scale of Buncefield, Texas City and Macondo in future. Such events have intensified
focus on functional safety management, leadership, key performance indicators and competence in
recent years, however incidents are still occurring.
Furthermore with the current industry pressures and the sharper focus on budgets, functional safety
performance is being threatened by the interminable rise of the silo factor - an inability within
functional safety management circles to collaborate and be consistent across all departments involved
in the lifecycle.
There are clear economic benefits from tackling the silo factor - for example not over specifying
equipment, reducing the amount of in-service testing and inspection, more efficient sharing of
functional safety lifecycle information and not duplicating efforts within the different phases of the
lifecycle.
This paper builds upon the broader PSM white paper produced by Conrad Ellison and Graeme Ellis of
ABB Consulting, by looking at specific Functional Safety Management (FSM) issues which arise if a
collaborative approach is not taken.