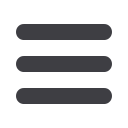

Page
1
of
10
Safety by Certificate – What happens when the Regulator says ‘No’ to
your SIL 2 certificate?
Paul Lucas, Principal Consultant, ABB Consulting, Belasis Hall Technology Park, Billingham TS23 4EB
Abstract:
In the process sector, hazards that have the potential to pose a high level of risk are
commonly protected by safety instrumented systems. For many years redundant systems have been
used to protect against the highest risks. This concept is embraced in the Functional Safety
Standards as the Hardware Fault Tolerance (HFT) requirement.
In recent times, manufacturers have utilised advances in technology by embedding intelligence
within the equipment enabling self-checking to be performed. The extent of this self-checking
influences what is called the Safe Failure Fraction (SFF). The advantage of this approach is that
high risks can be protected by single instruments, for example a SIL 2 can be protected by a single
device if the SFF > 90%. Information on the SFF is detailed on the manufacturer’s SIL Certificate.
ABB has been working with an end-user who assessed the risks for their storage tank and
concluded that SIL 2 overfill protection was required. The engineering contractor purchased a
single SIL 2 Certified Radar level gauge as the sensing element. Following a routine inspection by
the regulator, the end-user was asked to provide information to justify the performance of their
overfill protection. This information, including the SIL 2 certificate, was provided but rejected by
the regulator as not showing sufficient HFT.
On closer inspection, the device had a SFF below the threshold for SIL 2 and compliance was
claimed by ‘prior use’. The regulator requested details to support the prior use claim and again
rejected them stating that the data was 10 years old and did not differentiate between model
variants and software revisions.
The engineering contractor and end-user thought they had bought a SIL 2 solution because the
equipment had a SIL 2 certificate.
This paper will use this example to revisit the requirements for SIL 2 compliance to try and
understand the regulators decision, its implications for end users, and if the proposed changes in BS
EN 61511 Ed 2 would affect this decision.
Introduction
In the UK, owners and operators of high hazard process plants are regulated by the Control of Major
Accidents and Hazards regulations (COMAH, 2015). A key feature of the COMAH regulations is that
every operator shall take all necessary measures to prevent major accidents and limit their
consequences to people and the environment and reduce the risk of these accidents to ‘As Low as
Reasonably Practicable’ (ALARP).
In practice this means that the owner or operator: -
·
Must identify the potential hazards
·
Must quantify the risk posed by the hazards
·
Must demonstrate that the risk has been reduced As Low As Reasonably Practicable
Where the risk of the potential hazardous event is too high, then additional risk reduction measures
are required. These risk reduction measures may take many forms; for example reduced inventory,
remove sources of ignition, use less hazardous materials and installing instrumented systems.
Where instrumented systems are used for risk reduction, the current best practice in the process sector
is IEC 61511 (IEC, 2003), in the UK this is BS EN 61511 (BSI, 2004). The use of instrumented
systems to provide safety is termed ‘Functional Safety’ and BS EN 61511 is one of a number of sector
specific interpretations of the ‘parent’ functional safety standard, BS EN 61508 (IEC, 2010).