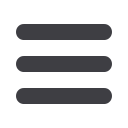

Institute of Measurement and Control Functional Safety Conference 2016
Challenges in Achieving Safety Instrumented Function Response Time for a Fast-Acting Process
Page 6
The industry rule of thumb is to select the SIFRT as half of the PST.
For rapidly developing hazardous cases which would result in a short PST, the target relationship between
PST and SIFRT is a major consideration, because the resulting calculated SIFRT may limit the number of
viable options and influence the design of the SIF components. For example, in the case study in which
the PST was calculated to be 30 seconds; if the relationship of SIFRT = 1/2 PST is used then the SIFRT
would be 15 seconds. If a 50% margin is used as per the operator guidelines, then the SIFRT would be 20
seconds. This 5 second difference can influence the technology selection for sensors and final elements.
There is no clear guideline for the design margin between PST and SIFRT in the industry standards.
Because of this, it can be overlooked throughout the project lifecycle phases. The design margin between
PST and SIFRT applied to the design should be established during the initial project phases and clearly
documented in the SRS.
Device Response Time
As stated in the previous section, to determine the SIFRT, the response time of each device in the SIF
must be known. The sum of all response times in the loop from initiator to final element will be the total
response time of the loop.
In the paper example, the initial proposed SIF from the project concept phase consisted of temperature
detection in the portion of the pipeline that would be exposed to the cryogenic temperatures which would
initiate closure of emergency shutdown valves located on the same section of pipe. Initially, this solution
was thought to be most suitable because it was the most direct measurement of the consequence and
hence provided protection against all scenarios that would lead to a cold temperature within the line.
Furthermore, it could be easily installed as part of the project.
On completion of process safety time calculations, however, it was determined that for some scenarios,
there was a rapid drop in temperature in the pipeline and thus an investigation into the suitability of a
temperature sensing device as the initiator was conducted. It was found that for the fast-acting scenarios,
which were caused by liquid carryover, the response time of the temperature loop was not fast enough and
a level loop was more suitable. In addition to this, the response time of the valve, which is typically the
slowest element to respond, was an area of focus. This section will discuss the challenges faced in
selecting devices and SIF architecture for the fast-acting loop and provide general discussions on the gaps
in determining SIF response time.
Methods of Measurement
Similar to process control loop strategies, the safety loop selection is done by determining the most
suitable measurement method – temperature, pressure, level - to mitigate a dangerous event. In process
control, the following rule of thumb is used for determining control loop strategies. Flow and liquid
pressure typically display no dead time and fast and noisy characteristics; gas pressure loops display no
dead time with slower characteristics; liquid level and temperature display variable dead time and
characteristics. For sensing elements, the response time of the instrument is the time between a change in
the process being measured and obtaining a resultant output. It is measured by the time constant, which is
the time required for the output to complete 63.2% of the total rise (or decay) resulting from a step change