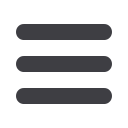

To be less skeptical we could take the view that today’s savvy process and functional safety related
personnel are on the ball. Executive leadership is at the forefront of safety improvement. Safety is the
first subject in every meeting (and not just holding the handrails or tidying up trailing cables).
Investment is forthcoming. The environment is ripe to grow a ‘safety culture’, where we challenge our
existing practices and continually strive to improve our performance. We’ll take a look at that view
during the tomorrow section of this paper.
The dial? Well all the relevant data is being processed, centralized, assessed, weighted, analysed and
verified and the indicator is way over in the green.
The EPCs and system suppliers take another view, that in order to compete and win safety related
work they must be able to prove they are capable and so emphasis a commercial view to assist sales.
There is also the worry of possible litigation should they deliver a safety system where poor design is
proved to be a factor in a major incident. Today, try a search on LinkedIn of personnel at any EPC or
top five suppliers with the word safety in their title, it’s quite an impressive list.
But here we are only looking at projects and project execution and the analysis and implementation
phases are short-lived compared to the long-term ownership and care of a live plant. There is still,
today, a disconnect between project delivery and the operations and maintain phases of the safety
lifecycle. After installation and commissioning phase, who is responsible for functional safety
management?
Again a well defined and managed functional safety plan helps immensely, not only
tracking our progress but allowing all team members to understand the whole process and how there
earlier activities have been built upon or just for the team to appreciate the bigger picture (no silos).
Tomorrow
As we look forward to how tomorrow may evolve, we mentioned ‘visibility, ‘openness’, if the whole
workforce is reminded of process safety every day, they can see the rewards of good or best practice
and understand how these practices are not only lowering risk but adding to the profitability and
competitiveness of the plant then a safety culture is more likely to flourish.
We have also considered the well-established area of asset integrity against the more recently
accepted practices of functional safety. We could actually break this into three sections asset integrity,
process safety management and functional safety management. There are numerous Process Safety
guidelines from bodies such as the Energy Institute and IChemE. The 61508 Association has a free
download which compares PSM and FSM and argues that PSM and FSM are largely the same.
They do however, argue, ‘why we should do things twice’? The philosophy of all three disciplines is
clearly the same and yet different groups using diverse data (or the same data diversely), different
practices and sometimes no communication between departments whilst going about their business.
As we move forward a phrase that is mentioned more and more is ‘big data’. The idea being that in
the event of there being extreme amounts of diverse data a team of switched on individuals using the
latest computer gadgetry and leading edge deep data delving algorithms can spot patterns and
anomalies which give a different insight into our lives and how we can predict trends.
In the world of process plants we could argue that we have a huge amount of data already and to a
degree we already understand the data it’s just who, where and how we use it, whilst considering our
ultimate objective of running highly efficient ad robustly safe process plant. Let’s not confuse the
quantity of data with the quality of information it provides.
What do we want to know from top floor to shop floor? We want to know we are operating safely, to
the best of our ability. We want to know every day that we are working in a safe environment. We
want to know that our efforts are not unnoticed and the safety and plant performance are at an