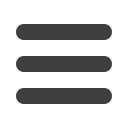

58
N
ovember
2010
www.read-tpt.com›
T
echnology
U
pdate
THE capabilities of machines for tube
processing have developed significantly in
recent years, especially due to innovations
in design concepts and control software.
At international trade shows machine
manufacturers present solutions to problems
that were deemed impossible as little as
ten, even five years ago.
But even the most innovative and capable
machine is dependent on accurate data in
order to attain its full potential. The software
applications by 3R software solutions are
designed to assist the user at every part of
this process, either as stand-alone programs
that augment existing IT-structure, or as
integrated software framework.
One of the first tasks when designing a
pipeline system is to draw up the schematics,
to see where it fits into the overall project.
RONIR2D is one of the programs used
for this purpose. It automatically classifies
all used components, including their material
and nominal diameters, and creates a symbol
key based on the included elements. It also
automatically generates bills of material for
purchasing and the construction department,
and assigns a logical and unique number
to each component of the diagram. The
application uses a database to store
element information, and thus it is possible
to calculate eg the weight of a particular
tube, or the centre of gravity of the entire
system. The system can also be tested
for logical consistency, and automatically
blocks the user from accidentally using
incompatible materials. Using the integrated
export function it is possible to save the P&I
diagram in different formats, so it can be
used in the next step in the process.
The construction department has the
task of turning the two-dimensional P&I
diagrams into three-dimensional pipeline
systems. This is usually done by splitting the
entire system into segments, and creating
isometric drawings (isos) for each of them.
These drawings can then be subdivided
into smaller sections (spools), which can
be manufactured in the workshop and
assembled on-site.
RONIIsoBuilder is designed to not only
create these isos, but also to import them
from a variety of third-party platforms. Since
RONIIsoBuilder focuses on pipeline elements
and fittings it offers a large range of features
specifically designed for the tube industry.
One major advantage of RONIIsoBuilder
is that all fabrication-relevant data can be
extracted from the iso, and do not have to
be calculated manually. Besides worksheets
and part lists for every drawing itself, it is
possible to create individual worksheets
and lists for every spool composing the
drawing. The actual cutting length can be
determined, and CNC-data for the various
machines in the workshop, such as the
bending machine or the flame-cutting
machine can be calculated.
In order to determine if a spool can
be fabricated with the existing machines
and tools, a bending simulation program
like RONIKolli7 is indispensable. By
creating virtual models of the machine
and all associated tools, it is possible to
test a tube for collision with the machine,
the tool, or the environment. In case of
interference the software can automatically
look for alternatives within the capabilities
of the machine and following customisable
parameters. The more complex the machine,
the more options the program has: simple
three-axis benders for example may allow
a reversal of the rotation direction or the
bending order, as well as a correction feed.
Besides a mere simulation of the bending
process RONIKolli7 offers features for
flange bending and the calculation of flange
displacement, cycle time approximation,
functions for the creation of tube coils and
segment bends, and the consideration of
material traits, to account for springback
and traction reductions. A newly developed
optional feature enables the user to create
models of customised tools for very
complicated bends. The CNC-data required
to fabricate the tube can be printed out
on worksheets or in many cases exported
directly to the bending machine. Often all
that is required of the machine operator is
to load the tube into the machine, confirm
the data on his screen, and supervise the
bending process.
Once the entire system has been divided
into sections and spools, these spools have to
be manufactured. Here it is important to both
minimise the need for manual calculations
and to arrange the order of the spools for
fabrication to reduce changeover times at the
various machines.
The 3R RAMP system consists of a
core application and various modules, each
of which controls one of the aspects of
fabrication. Data generated from isometric
drawings in RONIIsoBuilder is bundled and
can be arranged into fabrication packets,
always considering machine utilisation and
available material. Cutting lists are optimised,
so the amount of scrap is reduced as much
as possible. Bending lists are created in
respect to tool changeover, to reduce the
time spent on this task. And since each spool
is assigned a unique number, the status of
every single component can be monitored
at any point during the fabrication process.
This way it is possible to analyse machine
utilisation, work flow and capacities.
While each application developed by
3R software solutions can be used as a
standalone product, the combination of
RONIIsoBuilder and RAMP can increase a
tube shop’s efficiency significantly. Controlling
the flow of material and the utilisation of
the various machines is another important
factor, reducing idle time at the machines
and increasing output. But in addition to
these four core applications that govern the
important tasks involved in designing and
fabricating tubes, 3R software solutions also
offers various other applications designed to
facilitate various processes:
Like every other component of a
mechanical system, pipes break down
over time. Whether due to impact damage
or simple corrosion, eventually a part of the
pipeline system will have to be replaced.
Here it becomes important to fabricate a
replacement that can be inserted into the
existing system precisely. If the original
data used to fabricate the spool is no
longer available, it becomes necessary to
measure the tube.
There are several methods of measuring
tube elements, ranging from optical
measurementwithmultiplecamerastocontact
or non-contact measuring with movable arms.
While RONIKolli7 offers import interfaces
to many of these systems, 3R software
solutions also offers an affordable measuring
system of their own with RONITubeFit.
The measured data can be transferred to
RONIKolli7 in order to calculate the required
CNC-data for fabrication.
Creating drawings of existing pipeline
systems is a task that often has to be
performed in environments that do not allow
the use of big workstations. Sketches drawn
by hand, however, are at risk of becoming
smudged or damaged and have to be entered
into the CAD platform manually.
With RONIDraftboard it is possible to
sketch tube systems on a tablet-PC, a
lightweight touchscreen computer that can
be used on-site, to create digital drawings.
Lengths can be entered, elements can be
placed, and worksheets can be created.
For further processing the drawing can be
exported to RONIIsoBuilder or RONIKolli7.
3R software solutions
– Germany
Fax: +49 2381 9724 711
Email:
c.tripscha@3-r.deWebsite:
www.3-r.deImproving tube shop efficiency