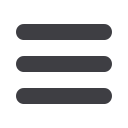

41
M
ay
2008
www.read-tpt.comT
echnology
U
pdate
›
of 72,000t and bends sheet plates with a
length of up to 18m (59ft) and a thickness
of up to 40mm (1.6").
Siempelkamp, Germany, supplied this press
to Baoshan Iron & Steel Co Ltd Shanghai
and put it into operation at a new plant. The
first pipe produced achieved all required
specifications and met the requirements of
the customer.
The sheet plates, which are bent into pipes,
are up to 40mm (1.6") in thickness. At a
width of up to 5m (16ft) and a length of 18m
(59ft), such a plate would take up an area
as large as a three-room apartment. The
plates weigh up to 25t, which is comparable
to the approximate weight of 20 passenger
cars.
The finished pipes have a diameter of up
to 1.42m (4.7ft). Around 500,000t of steel
plates can be processed on the press each
year. If the weight for the heaviest pipe
produced is assumed to be 25t, the capacity
for one year would correspond to a pipeline
length of 360km (224 miles).
The eight press cylinders, which were cast,
assembled and tested by Siempelkamp in
Krefeld, form pipes with a pressing force of
72,000t. These cylinders are installed in a
21m (69ft) long and 13.5m (44ft) high press
design.
The total weight of the press is
approximately 4,000t. Heavy parts such as
frames and press tables were manufactured
in China based on Siempelkamp drawings
and under Siempelkamp supervision. They
meet the contractual requirement for ‘local
content’.
Siempelkamp has built and upgraded
presses of comparable sizes many times.
Siempelkamp GmbH & Co KG
– Germany
Fax
: +49 2151 92 5683
:
ralf.griesche@siempelkamp.comWebsite
:
www.siempelkamp.comAssembly system
for diesel after-treatment
components
A leading provider of innovative metal
forming solutions, Hess Industries, has
developed equipment and systems for the
manufacture of diesel oxidation catalysts
(DOC), diesel particulate filters (DPF),
and selective catalytic reduction (SCR)
components and assemblies.
In 2000, the Environmental Protection
Agency
established
new
emission
standards for heavy-duty trucks and buses.
The EPA’s stringent diesel emission limits
for 2007-2010 reduce particulate matter,
carbon monoxide and hydrocarbon pollution
from heavy-duty highway vehicles by more
than 90 per cent.
The increase in governmental regulations
has created a growing demand for diesel
emission
after-treatment
products.
Hess, already a leading supplier of after-
treatment assembly systems for gas
engine applications, has expanded its
existing equipment designs to facilitate
the typically larger commercial diesel
designs. Part sizes with substrates up
to 13" diameter are typical, with larger
sizes available for off-road and special
applications.
Several systems and methods are offered
to assemble the converter substrate
(with support mat) into a stainless steel
tube or shell. These systems vary from
simple manually operated stations to
fully automated assembly cells for high
production. Due to the various methods
required to meet the individual customer
preferences and product designs,
Hess Industries offers a wide variety
of equipment to suit many different
applications.
Hess Industries Inc is a global
engineering firm and manufacturer
of metal forming machines, cells,
systems and factory automation
solutions with over 30 years of
experience. Hess also offers product
development
services
including
prototyping and short-run part
production.
Hess Industries Inc
– USA
Fax
: +1 269 683 1775
Website
:
www.hessindustries.comAdvanced straightening machines
for seamless tubes
Reika has received several orders for 6-roll-straightening machines for seamless tubes
from German, Spanish and Ukrainian customers. This follows on from the development
of straightening concepts for all areas of tube production.
The machines are equipped with special
features for seamless tube straightening
such as dry straightening, scale removal,
dust extraction, and special wear elements.
The machines have excellent design
features including solid ring frame, single
drives and CNC-control.
In addition, Reika has been awarded
many international contracts for complete
finishing lines for seamless tubes. Reika
again received a high number of visitors
to its Tube 2008 stand, which displayed a
high-speed cutting centre. Tube 2008 was
a record-breaking event.
Reika GmbH & Co KG
– Germany
Fax
: +49 2331 969036
:
info@reika.deWebsite
:
www.reika.de
Reika manufacture 6-roll straightening
machines for seamless tubes
Diesel exhaust
products from Hess