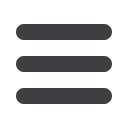

UPM Annual Report 2015
UPM Annual Report 2015
41
42
contents
in businesses such as common meetings with
contractors inWood Sourcing and Forestry,
a contractor safety programme in UPMPaper
ENAmaintenance operations and improved
safety in outsourced maintenance operations
in UPMTimber. The largest investment pro-
jects at UPMKymi, Finland and at UPM
Changshu, China had a strong focus on safety
with good results. There were only one LTA
accident at UPMKymi and no LTA contractor
accidents at UPMChangshu.
Health theme continued
To support the wellbeing of its personnel, UPM
is working in close co-operation with employ-
ees and external organisations who are respon-
sible for occupational health.
In 2015, UPM continued the health theme
that was originally launched in 2014 as the
“Focus on Health” campaign. The aim of the
health theme is to support continuous
improvement of employees’ health, quality of
life and ability to perform. In 2015, UPM
launched quarterly health themes, which were
recovery, physical activity, nutrition and brain
health. Several health and wellbeing initiatives
were launched at various UPM sites and busi-
nesses under these themes.
The “Personal Health Plan” project which
was piloted in 2014 continued at several sites
in Finland during 2015. This health project
consisted of a medical check, wellness assess-
ment and personal support based on individual
health improvement action plans. According to
the self-evaluation, improvement of the well-
being targets during personal support was on
average from 4.2 to 6.7 (scale 1-10). The annual
employee engagement survey (EES) results
also correlate with positive development.
To improve wellbeing at work, UPM is
monitoring employees using several metrics
and indicators on a yearly basis. The indicators
include, for example, the annual employee
engagement survey (EES), follow-up of safety
and absence indicators and occupational
health checks aligned with national legal
requirements.
Safety is an essential part of UPM’s activities and business management
system. Equal safety requirements are applied to all employees as
well as to visitors and contractors working at the company’s premises.
All employees in Finland and Germany are represented by joint
employer–worker health and safety committees as defined in local
legislation. The aim of these location-based committees is to monitor
and advise on occupational health and safety issues and programmes.
IN BRIEF
STRATEGY
BUSINESSES
STAKEHOLDERS
GOVERNANCE
ACCOUNTS
2015 was the first year after the “Step Change
in Safety 2012-2014” initiative. The next step
is to take safety from campaign mode to com-
pany-wide culture. Positive development
continued in occupational safety indicators.
In 2015, UPM’s lost-time accident fre-
quency (LTAF, the number of lost-time work
accidents per one million hours of work) was
3.9 (4.4). The result is UPM’s best. At the end of
the year, 12 production units achieved more
than one year without any lost-time accidents.
In addition, TRIF (total recordable injury
frequency) improved in 2015 being 10.6 (11.6).
near misses are investigated using root cause
analysis. In 2015, a total of 47,121 near-miss and
safety observation reports were recorded.
In 2015, safety efforts concentrated on
avoiding the most common accident types like
slip, trip and fall accidents and hand injuries. In
addition, UPM improved contractor safety and
implemented actions based on a fatal accident
in 2014 as well as further developed the overall
behavioural safety.
In the new biorefinery in Lappeenranta,
Finland, safety was very high on the agenda
during the first operational year with the help
of external audits. At the beginning of the year,
there were some process safety incidents but
the operation was stabilised towards the end
of the year.
Safety work will continue to be one of the
key focus areas. In 2014, UPM set the new
short-term target: to achieve LTAF 3 by the end
of 2017. An additional target is to avoid fatali-
ties or serious accidents. The ultimate target of
the safety work is to ensure that neither UPM
employees nor contractors are subjected to
any risks when working at UPM’s premises.
Safety improvement initiatives continue
in all business areas. Many of the activities in
2015 will continue during 2016. The focus will
be on behavioural safety, full implementation
of UPM safety standards, contractor safety
improvement, reduction of hand injuries and
improvement of safety during lifting opera-
tions. Amajor effort was carried out as UPM
built a common environmental and safety
reporting system “One Safety”. Use of the tool
will be rolled out in spring 2016.
Efforts on contractor safety
UPM requires its contractors to follow safety
guidelines which enable them to carry out
their work safely whilst on UPMpremises.
The safety induction is a prerequisite before
starting work at a UPM site. By the end of 2015,
over 65,000 UPM safety inductions to contrac-
tors were completed.
In 2015, several contractor safety improve-
ment projects were carried out or initiated
Staying healthy with WASH
UPM wants to make sure that all its
employees, regardless of their country or
location, work in an environment that is as
healthy as possible. In line with this goal,
UPM is the first forest industry company
to commit to the WASH (Water, Sanitation
and Hygiene) programme launched by
WBCSD.
The programme requires companies to
monitor the water, sanitation and hygiene
conditions within their organisation and
to make any required improvements.
UPM joined the WASH programme in 2014.
The company sent out a survey to all its
production facilities enquiring about local
water, sanitation and hygiene conditions in
2015. All production facilities from around
the world responded to the survey and
evaluated whether conditions at their sites
could be improved. In 2016, a survey will
be sent to sales offices, followed by forest
management and wood sourcing teams
in 2017.
Tap water is fit to drink in most European
countries, but subcontractors working
at a plantation in South America, for
example, should always carry safe bottled
water to quench their thirst.
Similarly UPM analyses and manages the
opportunities and threats related to healthy
working environments. UPM’s significant
operating sites are not located in areas,
where employees face risks related to HIV/
AIDS, malaria or tuberculosis.
Read more:
www.upm.com/responsibility, www.upmbiofore.comIn addition to LTA, it includes modified duty
cases and accidents requiring medical treatment.
The safety of the external workforce improved
as well. UPM’s contractors had 92 lost-time
accidents (114 in 2014). Unfortunately, there was
a fatal contractor accident in 2015 at UPMopera-
tions in the UK during foresting work.
The rate of absenteeism due to sickness and
accidents at work was 3.7% (3.4%) globally.
Absenteeism due to accidents at work remained
at the same level as in 2014.
Good performance in safety is recognised
with company-wide safety awards. The 2015
UPM Safety Award of the best improver was
given to UPMChangshu paper mill for improved
safety culture.
In April, UPM celebrated the company’s third
Safety Week in connection with the World Day
for Safety and Health at Work organised by the
International Labour Organization (ILO).
Driving continuous
improvement in safety
Regardless of severity, employees and the exter-
nal workforce working for UPMmust report all
near misses and make safety observations. These
are reported, investigated and corrective actions
taken to prevent their reoccurrence. High-risk
Continued development in
UPM’s safety culture and performance
2011
2012
2013
2014
UPM Raflatac
UPM Paper Asia
UPM Paper ENA
UPM Plywood
Number of lost-time work accidents/
one million hours worked
2015
UPM Biorefining
UPM Energy
15
12
9
6
3
0
Lost-time accident frequency,
UPM workforce
5
4
3
2
1
0
2011
2012
2013
2014
UPM Biorefining
UPM Energy
UPM Raflatac
UPM Paper Asia
UPM Plywood
2015
UPM Paper ENA
Absenteeism due to sickness and
accidents at work, UPM workforce
% absence hours/theoretical working time
■
Accidents at work
■
Sick leave
2013
2014
UPM Raflatac
UPM Paper Asia
UPM Paper ENA
UPM Plywood
Total injuries/one million hours worked
2015
UPM Biorefining
UPM Energy
15
12
9
6
3
0
Total recordable injury frequency,
UPM workforce