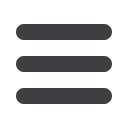

UPM Annual Report 2015
UPM Annual Report 2015
87
88
contents
accounts
IN BRIEF
STRATEGY
BUSINESSES
STAKEHOLDERS
GOVERNANCE
ACCOUNTS
Research and development in businesses
UPM Biorefining
UPM Pulp has continued to focus in improving the environmental per-
formance of its mills and its overall operational efficiency.
In UPM Fray Bentos, Uruguay, the consumption of process water
has been among the lowest in the industry. In the past years, special
focus has been in achieving a significant reduction of phosphor emis-
sions. The achieved low emission level makes it also in this respect a
benchmark in the industry. In all of its mills, UPM is now focusing on
solid waste reduction through a number of internal and external joint
research projects.
In Euca plantation operations in Uruguay, development work
focuses on the tree breeding program and development of new euca-
lyptus clones in order to create more value and improve productivity. In
Finland, special focus has been put on developing wood sourcing and
wood handling activities in order to reduce wood consumption at the
mills.
In the Pulp market side, UPM Pulp continued to focus, through its
Technical Customer Service support, on joint development activities
with customers, mainly in Europe and China, in order to enhance
cooperation and assure the best possible results when using UPM
Pulps.
In Biofuels, commercial production of UPM BioVerno renewable
diesel started in Lappeenranta, Finland in January, and the product
was launched successfully to the Finnish market together with St1 and
ABC fuel distributors. In March, UPM Biofuels was awarded the Com-
mercial Scale Plant of the year in the international WBM Bio Business
2015 competition.
As a product, UPM BioVerno was granted the Finnish Key Flag
Symbol due to its high domestic origin. The product was tested further
in several engine and fleet tests. UPM BioVerno was found to signifi-
cantly reduce tailpipe emissions, such as particle mass, hydrocarbon,
carbon dioxide, nitrogeous oxide and carbon monoxide emissions,
compared to traditional fossil diesel.
All the tests showed also similar or improved efficiency of the
engine, without compromising the engine power. The comprehensive
emission, performance and wear tests were carried out with a number
of key research institutes such as VTT Technical Research Centre of Fin-
land Ltd and at FEV, internationally recognised vehicle engineering
company based in Germany. To test UPM BioVerno in heavy duty vehi-
cles, UPM started field tests in urban buses in the Helsinki region bus
traffic.
In the long term, UPM aims to extend biofuel production to new
raw materials and processes.
UPM Energy
UPM Energy focused on improving the efficiency and cost competitive-
ness of biomass-based energy technologies. To reach its target, UPM
Energy participated in several research programmes. These pro-
grammes are creating knowledge to improve design and operation of
UPM’s large-scale energy conversion systems that use biomass fuel
mixtures. UPM Energy has also been evaluating the effects of Industrial
Emission Directive and BAT Reference Document which deal with large
scale combustion installations.
UPM Raflatac
In standard filmic and paper products the focus continued on the re-en-
gineering efforts for greater cost efficiency and product quality. In the
special business area the main emphasis was on developing new high
added value products for selected end-use segments, as well as tai-
lored solutions for specific customer needs. New sustainable catalyst
activated and UV curable adhesives were launched for the durable
goods end-use segment.
The development of new proprietary filmic materials continued.
Significant progress was made in the development of a shrink sleeve
label film especially designed for recyclable clear PET packages used
in the food and beverage end-uses.
UPM Paper Asia
R&D supports UPM Paper Asia businesses and operations in China
and Finland through development activities in its research centers in
Changshu and Lappeenranta. Main focus areas are in new product
development and operational efficiency.
UPM Paper ENA
Key focus areas of R&D activities for Paper ENA relate to developing
competitive products and product portfolios, top expertise in customer
support, variable cost savings and operational efficiency improve-
ments. R&D also supports in developing novel solutions for paper mill’s
waste & side streams management. Research centers serving Paper
ENA businesses and operations are located in Lappeenranta and
Augsburg and are equipped with state-of-the-art analytical capabilities.
UPM Plywood
UPM Plywood’s product management and development work focused
on creating new customer needs based solutions as well as piloting
and commercializing new products and applications developed previ-
ously. One of the key areas was to improve the properties of plywood
for end-uses such as the LNG carrier systems and Vehicle Flooring.
For concrete forming end uses, R&D work concentrated on creat-
ing a new product with innovative moisture barrier technology. Also
several new economic segment formwork panels were developed to
satisfy customer demands.
The development of fire retardant coated plywood was completed
and the product was introduced to the market.
Responsibility
Responsibility is good business
Corporate responsibility is an integral part of all our operations and is
seen as a source of competitive advantage. UPM is strongly committed
to continuous improvement in economic, social and environmental
performance. UPM promotes responsible practices throughout the
value chain and is active in finding sustainable solutions in co-opera-
tion with its customers, suppliers and partners.
In 2015, the main focus of UPM’s responsibility activities was the
renewal of the company’s Code of Conduct and responsibility targets.
The safety of employees and contractors also remained an important
focus area. UPM was invited to join the UN Global Compact LEAD
group intended for global sustainability leaders.
Environmental performance
In 2015, UPM’s environmental investments totalled EUR 28 million
(12 million). The largest being the investment to waste water treatment
and air protection at UPM Changshu paper mill.
UPM’s environmental costs, which were mainly attributable to efflu-
ent treatment and waste management, totalled EUR 129 million
(127 million), including depreciation.
No significant environmental incidents occurred in 2015. How-
ever, several minor temporary deviations from permit limits did arise.
These deviations were reported to the relevant authorities immediately,
and corrective and preventive measures were taken. These measures
are part of UPM’s internal Clean Run campaign that aims to improve
the company’s environmental performance further, sharing best prac-
tices and promoting and maintaining environmental awareness.
Prioritising product stewardship
UPM’s products are made from renewable, biodegradable and recy-
clable raw materials. UPM businesses have adopted an eco-design
approach in their product development processes, which means the
systematic integration of environmental aspects into product design at
an early stage, covering the whole lifecycle.
The majority of UPM’s production sites, as well as its forestry oper-
ations, are covered by environmental, quality and health and safety
systems, which are certified in accordance with the ISO 9001, ISO
14001 and OHSAS 18001 standards respectively. UPM has certified
all its European pulp and paper mills and the UPM Fray Bentos
pulp mill in Uruguay and UPM Changshu paper mill in China in
accordance with the voluntary EU Eco-Management and Audit Scheme
(EMAS). In 2015, the EU awarded UPM a recognition certificate for
being one of the pioneers of the 20-year-old EMAS scheme. UPM is
the largest producer of EU Ecolabelled newsprint, graphic and office
papers.
Reducing waste is part of circular economy
Today, approximately 90% of all UPM’s production waste is recovered
and recycled. UPM has developed innovative ways to reduce its own
waste and reuse waste or residues in new products such as UPM
BioVerno, UPM’s renewable diesel and UPM ProFi composite which
utilises partly waste from the production of self-adhesive label materi-
als. UPM is also the world’s largest user of recovered paper for the
production of graphic papers, consuming 3.1 million tonnes of paper
for recycling in 2015. The total amount of solid waste sent to landfill
has decreased with 9% compared to the previous year.
Sustainable forestry
All of UPM’s own forests and eucalyptus plantations are certified ac-
cording to the FSC and/or PEFC certification schemes. All of UPM’s
wood supplies are covered by third-party-verified chains of custody.
84% (83%) of all wood used by UPM is sourced from certified forests.
84% (83%) of UPM’s paper is produced using fibre that meets the
criteria of either the FSC or the PEFC forest certification scheme. Dur-
ing the year, UPM participated in the CBD Business and Biodiversity
Forum 2015 held in Helsinki. The CBD Business and Biodiversity Fo-
rum is part of the UN’s Convention on Biological Diversity initiative.
Climate actions and energy efficiency
Since 1990, specific CO
2
(fossil carbon dioxide) emissions per tonne
of paper have been reduced by approximately 21%. UPM has a wide
range of energy sources and it maximises the use of carbon-neutral
energy. Biomass-based fuels make up 83% of the fuels used by UPM in
Finland and 67% of those used worldwide. UPM is the second largest
generator of biomass-based electricity in Europe.
As the use of weather-dependent energy sources increases, the
need for balancing power in energy systems will also grow. UPM is
investing in hydropower, the most effective and sustainable method of
producing balancing power. UPM strives to continuously improve its
energy efficiency across all its operations. During the last 20 years, the
energy efficiency of production has significantly improved due to
energy audits, innovations and internal campaigns.
Water plays an increasingly important role
All of UPM’s pulp and paper mills are required to have both a mechan-
ical and a biological wastewater treatment facility. In order to ensure
the best possible treatment result and share best practice, UPM’s waste-
water treatment facility team has continued its work. The results have
been good and the number of incidents has decreased.
UPM has reduced wastewater volumes per tonne of paper by 16%
and per tonne of chemical pulp by 16% over the last ten years. The
COD load has decreased by 24% per tonne of paper, and by 41%
per tonne of pulp, over the last ten years.
UPM was the first forest industry company to sign the WBCSD
Water Cluster’s WASH Pledge programme. During 2015, access to
drinking and sanitary water has been determined at all UPM produc-
tion plants. This work will continue in 2016.
Corporate Governance Statement
UPM presents the Corporate Governance Statement as a separate
report which is available on the company’s website
www.upm.com.