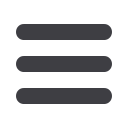

Wire & Cable ASIA – September/October 2007
56
Nove ber/De ember 2 13
www.read-wca.comStandard cables and similar products with a diameter of
minimum 4mm can be wound with very high quality. Steel
wires and steel tubes with even smaller diameters can also
be wound using the precision winding unit.
A prerequisite of a perfectly wound reel is that the reel
itself is of high quality. The better the quality of the reel, the
easier it is to achieve a satisfactory winding of the product.
Safety
Today it is sometimes necessary to manually guide the
cable onto the reel and this process can be both time
consuming and dangerous.
The person guiding the product will often have to focus
exclusively on the winding process, and depending on the
product he may have to stand immediately in front of the
take-up.
Standing close to the take-up involves the risk of being
jammed between the product and the reel, with serious
personal injuries as a result.
As health and safety requirements become more stringent,
it is increasingly difficult to carry out the manual guiding
of cable in front of the take-up, because it is completely
fenced in.
Even when it is possible to manually guide the cable onto
the reel, the distance from the operator to the take-up may
prevent a perfect winding.
Pulleys
To achieve the best possible control over the product, it
is important to guide the product as close to the reel as
possible.
It is a key parameter to have as little distance from the
pulleys guiding the product to the reel as possible.
The product is guided through a set of pulleys, which are
dimensioned according to the diameter of the product.
Because of the compact size of these pulleys, the distance
to the reel can be minimised. Furthermore, the pulleys are
shaped so that they are able to position the product very
close to the flange.
The guide arm is fitted with sensors detecting and
measuring the distance to the flange, and these sensors
ensure automatic change of traversing direction when the
cable is next to the flange.
The software controlling the precision winding unit is
developed to optimise the quantity of product on the reel,
eg by avoiding large gaps at the flanges when changing
winding direction. During winding the guide arm turns 180
degrees so that the pulleys are always able to run very
close to the flange.
The flange detection system makes it superfluous to
key in new parameters when changing to another reel
size. The precision winding unit automatically adapts the
traversing to the mounted reel and it is not necessary to
change end-settings.
When a layer is completed and the next one prepared,
the guide arm moves up the ball rail by a distance equal
to the product diameter in order to keep the product in its
horizontal position.
The inlet of the precision winding unit consists of a
number of pulleys, which are mounted in a funnel position
and thereby apply a minimum amount of pressure to the
product, even though the line height changes as the reel
becomes full. Using the precision winding unit makes it
possible to fill the reel to the edge of the flanges.
Reels
It is important to position the product as close to the
flanges as possible. Generally, it is recommended
that flanges do not deviate more than half the product
diameter.
If, for example, a product has a diameter of Ø12mm,
the flanges must not be more than 6mm off (±3mm).
This means that the smaller the product diameter, the
higher the demand for perfect reels.
For a number of years Roblon has supplied take-ups
with integrated precision winding units, capable of
handling reels ranging from Ø380 to Ø1,400mm with
a max gross weight of 1,800kg, and winding products
ranging from Ø3 to Ø16mm.
Some of the take-ups have been in use for the last
15 years, winding steel wires with a minimum of
maintenance, and this underlines the durability of the
technology.
❍
❍
Guide arm
❍
❍
Inlet pulleys