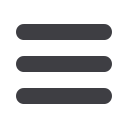

1/79
Articles marked ◊ are not held in stock, procurement is effected at short notice.
Cutting Tools
1
Design:
Ultra-finest grain-solid carbide, factory standard, type RT 100 T.
TiAlN coated surface, right cutting. Special slot form with double bevels,
special point geometry and special point thinning. With inner cooling.
Normal angle of rake 30°, core thickness thicker than normal and
without core gradient. The drill has a very good self-centring behaviour.
Application:
For drill holes
with very narrow ∅ tolerances
and very
good surfaces. Suitable for drilling extremely deep holes up to 20 x
D with high cutting speeds. Particularly suitable for short-chipping
materials such as cast iron, grey cast iron, malleable cast iron and
nodular graphite iron and aluminium alloys with a high silicon content.
Note:
The drills can be sharpened several times.
Order
No.
Steels
up to
850
N/mm
2
Steels
up to
1000
N/mm
2
Steels
up to
1400
N/mm
2
Steels
up to
42 HRC
Steels
up to
52 HRC
Steels
up to
56 HRC
Steels
up to
60 HRC
Hard
machining
over
60 HRC
Stainless
and acid-
resistant
steels (INOX)
Ti steels,
Ti alloys,
special
steels
Cast iron
materials
Al, Al and
Mg alloys
Copper,
brass,
bronze
1234
110
110
110
80
50
110
100
120
Order
No.
∅ m7/
h7
mm
1234
TiAlN
Spiral
length I
2
mm
Shank
length I
3
mm
Overall
length l
1
mm
Shank ∅
d
2
= h6
mm
6WHHOV
XSWR
1PP
f
mm/rev
0300
3.0 238.70
70 36 100
6 0.100
0350
3.5 238.70 ◊
96 36 136
6 0.125
0400
4.0 253.10
96 36 136
6 0.125
0450
4.5 281.90 ◊
118 36 158
6 0.125
0500
5.0 288.10
118 36 158
6 0.125
0550
5.5 300.50
140 36 180
6 0.160
0600
6.0 333.40
140 36 180
6 0.160
0650
6.5 362.20
162 36 202
8 0.200
(W114)
Order
No.
∅ m7/
h7
mm
1234
TiAlN
Spiral
length I
2
mm
Shank
length I
3
mm
Overall
length l
1
mm
Shank ∅
d
2
= h6
mm
6WHHOV
XSWR
1PP
f
mm/rev
0700
7.0 368.40
162 36 202 8 0.200
0750
7.5 399.30
183 36 223 8 0.200
0800
8.0 432.20
183 36 223 8 0.200
0850
8.5 475.40
205 40 249 10 0.250
0900
9.0 481.60
205 40 249 10 0.250
1000
10.0 481.60
227 40 271 10 0.250
1200
12.0 535.10
274 45 323 12 0.250
1400
14.0 761.50
318 45 367 14 0.315
(W114)
Deep hole drill, 20 x D
TiAlN
Design:
Ultra-finest grain-solid carbide, factory standard.
TiAIN coated surface, right cutting. Special slot form with double
bevels, special point geometry and special point thinning. With inner
cooling. Normal angle of rake 30°, core thickness thicker than normal
and without core gradient. The drill has a very good self-centring
behaviour.
Application:
For drill holes
with very narrow ∅ tolerances
and very
good surfaces. Suitable for drilling extremely deep holes up to 25 x
D with high cutting speeds. Particularly suitable for short-chipping
materials such as cast iron, grey cast iron, malleable cast iron and
nodular graphite iron and aluminium alloys with a high silicon content.
Note:
The drills can be sharpened several times.
Order
No.
Steels
up to
850
N/mm
2
Steels
up to
1000
N/mm
2
Steels
up to
1400
N/mm
2
Steels
up to
42 HRC
Steels
up to
52 HRC
Steels
up to
56 HRC
Steels
up to
60 HRC
Hard
machining
over
60 HRC
Stainless
and acid-
resistant
steels (INOX)
Ti steels,
Ti alloys,
special
steels
Cast iron
materials
Al, Al and
Mg alloys
Copper,
brass,
bronze
1235
100
100
100
70
50
100
130
110
Order
No.
∅ m7/
h7
mm
1235
TiAlN
Spiral
length I
2
mm
Shank
length I
3
mm
Overall
length l
1
mm
Shank ∅
d
2
= h6
mm
6WHHOV
XSWR
1PP
f
mm/rev
0300
3.0 261.40
85 36 125
6 0.100
0350
3.5 261.40 ◊
116 36 156
6 0.125
0400
4.0 281.90
116 36 156
6 0.125
0450
4.5 316.90
143 36 183
6 0.125
0500
5.0 329.30
143 36 183
6 0.125
0550
5.5 343.70 ◊
170 36 210
6 0.160
0600
6.0 393.10
170 36 210
6 0.160
0650
6.5 405.40
197 36 237
8 0.200
(W114)
Order
No.
∅ m7/
h7
mm
1235
TiAlN
Spiral
length I
2
mm
Shank
length I
3
mm
Overall
length l
1
mm
Shank ∅
d
2
= h6
mm
6WHHOV
XSWR
1PP
f
mm/rev
0700
7.0 413.70
197 36 237 8 0.200
0750
7.5 458.90 ◊
223 36 263 8 0.200
0800
8.0 500.10
223 36 263 8 0.200
0850
8.5 545.40 ◊
250 40 294 10 0.250
0900
9.0 607.10 ◊
250 40 294 10 0.250
1000
10.0 607.10 ◊
277 40 321 10 0.250
1200
12.0 699.70
337 45 386 12 0.250
(W114)
Deep hole drill, 25 x D
TiAlN
RT 100 T method:
• Mill a surface at right angle to the start angle of hole machining.
• Produce a cylindrical pilot hole (tolerance F9) with a drilling depth
of at least 1 x D.
• Insert into the pilot hole with approx. 300 rpm at f = 500 mm/min.
• Set the cooling lubricant pressure and speed.
• Continual drilling to full drilling depth without relief cycle.
• When drilling through holes with oblique exit, reduce the feed rate
v
f
to 40% ca. 1 mm before breaking through.
• After reaching the drilling depth, switch off the rotation
and coolant, extract in rapid traverse.
• Conventional coolant lubrication min. 40 bar
Note:
The drills can be sharpened several times.
All deep holes must be piloted before starting to drill.
Deep hole drills should never be moved freely in the
machine when at the full speed.
Solid
carbide
Factory
standard
Type
RT
100 T
DIN
6535-HA
135°
20xD
Solid
carbide
Factory
standard
Type
RT
100 T
DIN
6535-HA
135°
25xD
3
3
Drilling tools
97