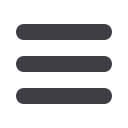

Industry News
www.read-tpt.comN
ovember
2015
15
• Heavy duty components for robust machines
• Long term operation in demanding environments
• Full range of machines from 3/16
(
to 3
(
OD
• End-forming, grooving and crimping machines
• Full range of equipment and tooling options
• In-house SPC and development lab
• Pre-shipment run-off on your parts
• ISO 9001:2008 registered
Find out how Manchester equipment can improve your
productivity and bottom line. Call 260-982-8524 or visit
our website today. Reps wanted in Europe and Asia.
Manchester
Tube End Forming
Equipment and Tooling
www.mtdtube.comExceeding
expectations
since 1960.
Annealing line for stainless steel
precision tubes
TUBING in the small diameter range
below 1" OD is commonly used in
specialist applications in the medical,
aerospace, automotive and precision
equipment sectors. These applications
can demand tubing with the highest
standards in terms of mechanical and
surface quality.
Plasmait has completed the building
of an annealing and surface treatment
line for a producer of precision tubing,
which involved a custom-built coiler
type payoff and take-up, and covered
an OD range from 0.5 to over 8mm. The
annealing and surface treatment line will
be used primarily for various stainless
steel and nickel alloy tubing, but will also
be capable of producing other materials
with a wide annealing temperature
range from 300°C to 1,200°C.
The line has been built for a producer
of small size precision tubing whose
prime concern was the quality of
recrystallisation, as well as
clean, bright and scratch-free
finish of the tube surface.
Plasmait’s heat and surface
treatment solution not only
met the client’s stringent
quality requirements of
finished material, but also offered a
modern, computer-controlled facility
designed for ease of use and minimal
environmental impact.
The new facility occupies a fraction
of the space that would be required
by a conventional multi-line annealing
furnace of the same capacity. The
annealing line features high energy
conversion efficiency, low purging
gas consumption, quick string-in, and
computer-based quality control.
PlasmaAnnealer can cold start
production in a few minutes, and can
be stopped immediately. This avoids
lengthy heating-up and cooling-down
times and associated energy costs
that are symptomatic of a conventional
furnace.
Ion sputtering on the material surface
results in dry surface degreasing and
surface oxide removal, which have
proved beneficial to applications with
demanding
surface
requirements
in sectors such as medical, heat
exchanger, food processing, chemical,
aerospace, aviation and automotive.
Plasmait GmbH
– Austria
Fax: +43 3182 52 4754
Email:
info@plasmait.comWebsite:
www.plasmait.comPlasmait’s
PlasmaAnnealer