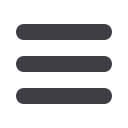

Technology News
www.read-tpt.com60
N
ovember
2015
Solution for combined pipe forming
THE technical challenges of modern
pipe processing are constantly
increasing, driven by demanding
applications for high grade piping. A
singlemanufacturing process is often not
enough to perfectly and effectively form
pipe ends, requiring interaction between
combined axial and rotary pipe forming
techniques. transfluid Maschinenbau
engineers have developed a new range
of combination machines to achieve
this.
Managing
director
Stefanie
Flaeper explained the improvements
incorporated: “There are actually
five fundamental changes. For a
start, our combination machine is
now externally more compact. All the
drives are electrical, and CNC control
enables synchronous axial and radial
movements. And we have once again
made significant improvements to rotary
forming techniques. For the first time,
these techniques now enable forming
of contours virtually independent of the
tool. Our machines are furthermore also
now CNC controlled and it is possible to
very effectively form pipes with bends in
excess of 90°.”
The new features of the combination
machines allow additional pipe
forming options. The swaging unit
can accommodate, for example, an
intermediate chuck, despite the electrical
drive. A wide variety of tools may be
used for various rotary forming tasks,
and the machines can also cut chipless
– from the inside out and vice versa.
Newly introduced CNC technology – as
with the transfluid stand-alone rotary
forming machines – allows contour
forming irrespective of the tool.
transfluid will be present at the
Blechexpo trade fair (3-6 November), on
stand 4000 in Hall 4.
transfluid Maschinenbau GmbH
–
Germany
Fax: +49 2972 9715 11
Email:
sales@transfluid.deWebsite:
www.transfluid.deContinuous tube cutting
THE first bandsaw from the new
KASTOwin range to be purchased in
the UK was delivered directly from the
launch at Kasto’s Milton Keynes open
house to Dyn-Metal, a specialist bronze
foundry and machine shop in Acton,
north-west London.
Since the machine was installed in
August 2014, it has been the mainstay
of the firm’s long production runs of
automatic sawing-to-length of bronze
tube, used principally in bearing
production. The material is used in
ships’ transmissions, oil and gas rigs,
off-road vehicles, cranes, steel mills,
mining equipment and machines in
general, including machine tools.
The bronze alloys are produced
in six centrifugal casting machines
at the Acton foundry, one of which is
among the largest in the UK, capable
of producing two-tonne castings. The
phosphor-, lead-, aluminium- and
manganese-bronze tubes can be
cast up to 1.2m in diameter, although
larger is possible depending on length
and weight. However, most material is
below 330mm, which is why Dyn-Metal
chose a KASTOwin A3.3 bandsaw of
that capacity.
Managing director Stephen Capper
said: “We supply standard bronzes as
well as our own special varieties with
modified grain structures, which result
in bearings lasting up to three times
longer than commercial castings of
similar composition. Self-lubricating
varieties with embedded solid lubricant
are included in our range.
“We needed another horizontal
bandsaw to replace an older model
of a different make that was causing
bottlenecks, as our order intake has
returned to pre-recession levels.
When I saw the new KASTOwin at
the supplier’s launch, the machine’s
competitive price, small footprint and
ability to tackle long automatic runs
made up my mind on the day, so I
placed the order for the machine there
and then.”
Kasto Ltd
– UK
Website:
www.kasto.uk.com