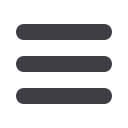

N
ovember
2015
85
Sikora AG
Article
X-ray scanner for pellet, flakes
and film inspection and analysis in
the compound, masterbatch and
recycling industry
By Dr C Frank, Sikora AG, Bremen, Germany
Introduction: Rising quality
demands and challenges in the
plastic industry
For industrial production, highly pure and flawless plastic
material is an important quality aspect. Due to the continuously
increasing requirements, it is necessary to detect and monitor
defects and impurities of decreasing size in plastic and
intermediate products. Impurities of 50µm may already cause
damage to production systems, such as to the crosshead
of the extruder, or to the end products, with high follow-up
costs. An example can be taken from the cable industry.
For the production of a high-voltage subsea cable, it is of
crucial importance to use highly, or so-called super clean,
material.
A contamination which enters the cable during production can
lead to a massive failure
[1]
of the cable once it is positioned very
deep under the sea level. It costs millions to repair a broken
subsea cable. For the cable industry, it is especially important
to detect metallic contaminations before the material is used
for final production. Therefore, latest norms and standards,
such as the Chinese standard IEC 62067 (for 150-500kV) for
high voltage cables, demand the exclusion of contamination
from 75µm in the processed material
[2]
. However, not only
the cable industry has these requirements. Other industries,
such as the medical, hose and tube or car industries, have to
monitor and analyse the quality of their used material.
The quality standards in the plastic manufacturing
industries are permanently increasing. Therefore, plastic
material has to be inspected and analysed for different
types of defects before it enters the final product.
Contamination, defects or inhomogeneities down to a
size of 50µm in the material have to be detected. This
is achieved by a modular X-ray scanner and analysis
equipment that can either be used continuously “at-line”
or for sample testing. In this way, transparent, opaque,
coloured or black pellets and flakes as well as thick
coloured films and tapes can reliably be inspected and
analysed. Consequently, highest material purity and
stable production processes can be assured.
In the different processing steps for the production of plastic
products, defects may repeatedly occur. This affects the
processes of material producers as well as the compound and
masterbatch producers, the processing industry, the recyclers
and the whole supply chain. Accordingly, it is necessary to
control and monitor the quality of the material used before it
is further processed.
In an industrial process in the plastic manufacturing industry,
it is possible to find many different types of possible defects
which enter the end product. These different types of defects
can have different effects on the final product.
Here we can distinguish between visual effects, but also
effects on the functions of the end product as described, for
example, in the cable or medical industries. Defects can also
cause damage to highly sophisticated processing machines
such as an extruder or injection moulding machine.
Picture 1: The X-ray analysis
shows two contaminants within
a round pellet
Picture 2: Different pellet
type is visible due to
higher X-ray attenuation