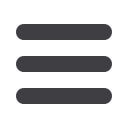

have expended a large amount
of effort and energy on putting
systems in place to allow the com-
pany to grow.
“Having all this technology
and skills available to us, it makes
absolute sense that we drive the
technology. Naturally it is an in-
tensive process, as it requires the
input of everyone in the company.
It requires testing, research and
development and, where neces-
sary, acquiring new skills.”
An example of PMSA’s ongoing
product development is its new
Eco range of automated handling
systems, unveiled at Totally Con-
crete 2016. This latest technology
gives customers the option of au-
tomated handling plants at a far
more affordable price compared
to top-of-the-range systems.
The new Eco range of handling
systems includes forklift options
as opposed to more conventional
but higher-cost finger and transfer
car systems. With the largest fully
automated PMSA machinery over
165 000 bricks can be made with
as little as nine people in a 9-hour
production shift. So while the
capital cost increases the actual la-
bour cost per block is dramatically
reduced. This results is labour
savings as much as 80% or more.
Ebeling concludes, “With the
new mass housing projects the
cost control of input products is
of vital importance and industrial
machinery will be required to pro-
duce high volumes of affordable
houses. This requires more effi-
cient use of equipment, labour and
materials to enable government to
roll-out more houses with a fixed
budget. The real job creation is
then created in the building of
more houses with the same set
budget.”
PMSA brick-making machinery
produces two million bricks a day
in the Johannesburg area alone.
■
and innovation
ʻWith the new mass housing projects the cost
control of input products is of vital importance and
industrial machinery will be required to produce high
volumes of affordable houses.’