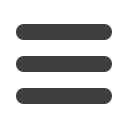

5
4
3
1
2
1114
ÖLFLEX
®
ACCESSORIES
FLEXIMARK
®
SILVYN
®
SKINTOP
®
EPIC
®
HITRONIC
®
ETHERLINE
®
UNITRONIC
®
APPENDIX
For current information see:
www.lappgroup.comT4
Technical Tables
Assembly guidelines
1.
The delivery drum must be transported as close as possible to the
installation location. Avoid rolling the cable drum unnecessarily. If it
is not possible to transport the drum directly to the system, we
recommend unreeling the cable from the drum using guide pulleys.
A drag rope and a cable grip should also be used.
2.
The cable can only be unreeled using cable stands or unwinders and
only from above. When doing so, the cable must also be stretched
out straight, and must not be deflected or pulled over any sharp
edges. The cable temperature should not fall below +5 °C during this
process (Lapp’s recommendation).
3.
The entire length of cable must be laid out prior to installation.
Avoid rewinding the cable from the delivery drum directly onto the
unit drum. When laying the cable, avoid “S”-shaped bends or other
similar deflections. The cable must be free of twists when wound on
the unit drum. Likewise, it must be possible to connect and fasten
the cable to the feed-in point without any twisting. (fig.
1
).
4.
The core layer structure of windable ÖLFLEX
®
CRANE cables has an
“S”-shaped core stranding design. We therefore strongly recommend
that you ensure the first layer of the cable is wound onto the drum
in the correct direction, depending on the feed-in position of the
cable alongside the drum body, as shown in the figure
2
. Other-
wise the cores could become damaged.
5.
If a feed-in point is passed over during operation, a pulling protec-
tion drum with the correct diameter should be used underneath
the travel path. At least 1-2 cable windings should be placed on
this drum in order to evenly distribute the tensile forces. A deflec-
tion funnel with a defined radius should be applied above the
drum.
6.
To fasten the cable to the feed-in point, it is absolutely necessary
to use sufficiently large clamps or cable support grips in order to
ensure cable-friendly strain relief. The clearance between the
fastening and the drum should be at least 40 x D.
ÖLFLEX
®
CRANE NSHTÖU, ÖLFLEX
®
CRANE VS (N)SHTÖU and ÖLFLEX
®
CRANE PUR
7.
With a fully unreeled cable, at least 2 cable windings should remain
on the unit drum to provide strain relief.
8.
The bending diameter for ÖLFLEX
®
CRANE NSHTÖU, on cables
with an outer diameter of up to 21.5 mm, must not be less than
10 times the cable diameter, and 12.5 times for cables with larger
outer diameters.
With ÖLFLEX
®
CRANE VS (N)SHTÖU and ÖLFLEX
®
CRANE PUR, the
bending diameter must be at least 15 times greater than the cable
diameter. The relevant minimum bending radius is listed both on
the corresponding catalogue page and the product data sheet.
9.
“S”-shaped bends in the cable should be avoided during operation.
However, if this is not possible, the space between the deflection
pulley axes must be at least 20 times the cable diameter for cables
with an outer diameter of less than 21.5 mm, and at least 25 times
for cables with larger outer diameters.
Cables which are suitable for this application are listed in selection
table A3-2. (fig.
3
).
10.
For the installation and operation of the cables ÖLFLEX
®
CRANE VS
(N)SHTÖU and ÖLFLEX
®
CRANE PUR, the maximum tension load of
the cable should be observed for each dimension based on the
integrated supporting elements (see product page in catalogue).
For cables with large outer diameters (approximately 21.5 mm and
above), we recommend using guide pulleys to minimise friction on
the outer sheath when changing direction. (fig.
4
).
11.
In order to prevent the cable from twisting, the inner contact
surface of the pulley must not have a concave shape. To ensure
that the cable runs smoothly, the inner width of the guiding groove
must be at least 10% greater than the outer diameter of the cable.
(fig.
5
).
12.
These cables fulfil the requirements stipulated by VDE 0250 and
VDE 0298-3 (use/installation). Any loads exceeding those specified
will reduce the service life of the cable:
INCORRECT
INCORRECT
INCORRECT:
Pulley
CORRECT:
Pulley