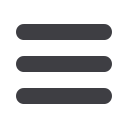

EuroWire – July 2007
62
english technology news
Spark tester – choose
with care
Spark testers have become essential
instruments in the field of electric wire and
cable insulation control. There are many
factors to consider when choosing a unit.
When manufacturing a wire or cable, it is
important to know its destination country,
as there are regulations and standards
(BS, CEI EN, CSA, MIL, UL) formulated by
a large number of organisations, and
different operating standards for spark
testers. The introduction of global quality,
recurrent certifications of the product’s
measuring and testing equipment, CE
data monitoring and EC marking have
all created new equipment manufacture
requirements.
Cable manufacturers, in order to maintain
their quality standard, have introduced
the spark tester not only along extrusion
lines but also throughout all other
production processing activities. This
has made it possible to track a product
step by step, find faults and take action
on machine parts that cause these faults,
preventing manufacturers from learning
that the product is faulty only at the end
of the manufacturing process.
Process automation and product data
acquisition have become essential to
avoid setting errors, to analyse production,
to search the balance point, and to take
preventative action on the systems to
ensure efficiency.
Communication among the various parts
of the system, through the use of high-
technology systems, is now an everyday
occurrence. Equipment that generally
used to operate through manual settings
entered by the operator, today needs
to be designed for automatic-control
operation, through the application of new
communication standards and protocols
(RS232, RS485, PROFIBUS, CANBUS,
Ethernet).
Before choosing a spark tester, multiple
factors need to be considered: reference
standards, maximum test voltage, AC or
DC, cable diameter, speed and, if AC, test
frequency. These choices could seem easy,
but cable manufacturers are often led to
make lower-end purchases, compared to
their real needs. This is due to the spark
tester manufacturer’s lack of information,
and the tendency to cut operating costs.
Other
aspects
that
are
generally
underestimated include:
The capacity of the wire or cable to
be tested. This aspect is normally
underestimated because it is generally
believed that there is little to choose
between different spark tester types.
People often think that, to avoid mistakes,
they should buy equipment featuring
maximum performance and, hence, the
highest frequency so as to comply with
all standards. Later, when they try the
product, they realise they cannot set the
desired test voltage or that non-existent
faults are detected. The foregoing process
leads them into a loop wherein they
cannot get to know how reliable the
machine is, and are forced to be happy
with rough test results.
Product assistance. A very important
element that is worth considering, as
an essential requirement concerns the
supplier’s organisation, and the response
time needed to solve the problem. Other
factors are whether service contact is
direct or indirect, the way the product
warranty is formulated, the time required
to take action and the related costs.
Unfortunately, all this only shows up
when the first fault occurs. It is therefore
important to consider factors like the
supplier’s solidity and how reliable the
organisation is.
Before and after-sale service. Most of the
time, the value of technical support and
advice the supplier can provide, along
with recurrent product certification, which
provide a guarantee for reliable data and
a product that is constantly kept under
control, are not taken into account.
In today’s market, where cost is an
important element, people often tend to
be blinded by a price that is apparently
low, but which hides a thousand snares.
Above all, it forces the customer to suffer
a penalty linked with the sale, instead of
receiving increased value from technical
advice that aims at supplying the best
product, whose real value added is the
expression of experience and know-how.
SIFMDC – Italy
Fax
: +39 035 4559358
:
info@sifmdc.comWebsite
:
www.sifmdc.comSTM spark tester
▲
Customised
solutions
in
coiling
systems is the hallmark of KFM
Kabelmaschinenfabrik Müller.
Founded in the 1960s, the company
is specialised in coiling and packing
machinery, but it has also developed
cabling machinery such as SZ-
stranders, binding heads and belt-type
meter counters. For coiled cable KFM
Kabelmaschinenfabrik Müller offers a
wide range of systems in the market of
automatic machines.
The RH Series machines cater for wire
and cable in diameters from 3mm to
25mm. Flexible and rigid, plastic and
rubber coils are possible from 200mm
outside diameter to 800mm outside
diameter.
These vary in height from 30mm to
300mm. The cable is tested before
winding and defect parts are eliminated
automatically.
The coils can be fixed with one
diametral strap or cord, 2 or 4 straps or
cords, or only with stretch foil.
This may be shrunk in foil if needed, and
is palletised on different sized pallets.
Features like automatic labelling with
real time printing, perimetral taping,
real time ink-jet printing or perforating
the foil for easy unwraping are possible.
For cable coiled on reels the company
offers about the same wide range of
possibilities. The TS-Machines have
been built for cable from 3mm outside
diameter to 25mm outside diameter.
For winding on, reels of about 125mm
diameter to drums of 1,000mm
diameter, made from carton, plywood or
sturdy wooden DIN-Drums are available.
The cable’s end can be fixed by a tape, a
strip of stretch foil or covered by stretch
foil. Each reel (drum) may get one or
more real time printed labels, and is
automatically palletised.
For both, the RH-lines and the TS-lines,
the manufacturer undertakes the best
quality and production speed.
KFM Kabelmaschinenfabrik Müller
GmbH – Germany
Fax
: +49 4498 293361
:
info@kfm-mueller.deWebsite
:
www.kfm-mueller.deSpecialised solutions to coiling problems