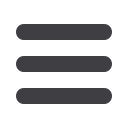

2016 REGISTRATION DOCUMENT
HERMÈS INTERNATIONAL
61
Corporate social responsability
2
Raw materials and suppliers
Footwear
Waste disposal was entrusted to a new service provider at the end
of 2016. Several new recycling solutions are being proposed.
Logistics
When handling products, each of the quality control agents wears a pair
of single-use textile gloves. During the campaign to collect clothing car-
ried out as part of Sustainable Development Week, a process to give a
second life to these gloves was launched: they will be reused for other
purposes during the processing activities of an external partner.
Construction
Since 2014 a proportion of the leather offcuts from leather goods
workshops is systematically used to cover counters in all stores and arti-
sans’ workbenches. In2015, the concept of thepop-up store, with re-use
of furniture, was rolled out to Europe, the Americas and Asia. In 2016,
window displays at the store in King of Prussia, Pennsylvania (US) were
decorated using objects created with leather offcuts from France.
Also in 2016, selective sorting and recycling of materials for stores or
stands being dismantled after their useful life had ended was organised
progressively to send the output to local recycling facilities. For example,
the annual display stand of La Montre Hermès at the clockmaking fair in
Basel, Switzerland, measuring approximately 1,000 m
2
, is rebuilt each
year using 80% recycled structural materials as well as the technical
equipment for lighting and the furniture from the previous year. The
remaining 20% of used materials (carpet, flooring, linoleum) goes to
local recycling facilities.
Furthermore, in France the Group has also defined and implemented a
methodology for recycling furniture that has reached the end of its life by
sending it to the service industry, working together with green organisa-
tions approved by theMinistry of Ecology and Sustainable Development.
2.4.4
Suppliers monitoring
Within the context of the Group’s monitoring plan, jointly led by the indus-
trial department, the audit and risk management department (A&RMD),
and the legal department, new concrete actions have been launched or
planned, while others have been expanded.
On the legal front, Hermès is formally asking suppliers for their support
in complying with its corporate and regulatory responsibilities. TheGroup
is also asking them to check their own suppliers, throughout their supply
chain, to ensure that they are fulfilling their obligations. The contract
clauses provide for the possibility of verifying that these undertakings
are real through an operational audit.
In terms of IT, there is a central platform. This tool makes it possible
to share all supplier data throughout the Company. Its purpose is two-
fold, hosting legal documents (agreements, commitments, etc.) from
partners and providing an overview of revenue.
With the support of an external firm, theGroup also carries out risk audits
(EHS, corporate, etc.) with its partners. These audits make it possible to
perform an on-site check of their commitments, ensuring that relevant
regulations are being complied with, and verifying the real working condi-
tions and well-being of their employees. These audits end with a shared
understanding and an action plan, where applicable.
Finally, the industrial department runs the network of purchasers for the
House, which operates andmaintains the information system serving as
the structure for these functions. It also carries out joint actions, such as
creating industry questionnaires in order to do preliminary diagnostics
on EHS compliance, implementing common rules to be used in filling
out questionnaires for new suppliers, and organising the sharing of this
knowledge through the entire network. Training is also prepared and
delivered by and for this network. The training pertains to the purcha-
sing policy of the Group, legal rules, and tools, but also relates to raising
awareness around risk and how to evaluate it.
The example of Tanneries
As part of the division’s commercial relations with its subcontractors and
hide suppliers, the industrial department regularly performs audits in
order to check that theGroup’s requirements – notably in terms of quality
as well as compliance with social and environmental commitments – are
actually being respected. At the end of 2015, more than 40% of the
partners had been visited. Over the last three years, 90% of them have
been audited.