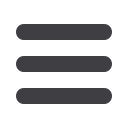

2016 REGISTRATION DOCUMENT
HERMÈS INTERNATIONAL
76
Corporate social responsability
2
Environment
(change of exchangers on the roof), optimisation of time slots and the
installation of motion detectors for lighting. The site also uses energy
supplied by photovoltaic panels.
Crystal
The processes using the most energy at the production unit are melting
the rawmaterial and working with it while hot. The best available techno-
logy in terms of production volumes is implemented in each investment
project. The two recently renovated furnaces are a prime example.
The reorganisation of themelt shop with its new tank furnace allowed the
pooling of energy-consuming equipment on workstations (e.g. openings)
and a reduction in the use of single-cell furnaces by optimising the use of
the pot furnace renovated in 2015.
The energy audit carried out in 2016 identified additional measures
to reduce consumption, particularly on equipment used “around the
edges” of the process, thereby confirming the interest of the blueprint
currently being carried out to replace some boilers.
Perfumes
The establishment of a system to recover heat generated by air compres-
sors now enables the production of hot water, which lessens the load on
boilers and in turn has a favourable impact on gas consumption.
Heat insulation has been installed or replaced on the pipes of air hand-
ling units and boilers in order to improve the efficiency of the equipment.
A campaign to replace existing lighting with LED systems in various buil-
dings, especially the warehouses, has just begun.
Construction
Improving energy efficiency in our stores means optimising the main
areas of energy consumption, which are lighting and air conditioning.
Lighting
Since 2013, an all-LED lighting solution for our watch and jewellery
window displays, shelving and ceiling lights has been extended to all
new store projects. In 2014, the retail projects department introduced
a range of LED bulbs specially developed for Hermès and suitable for all
existing installations and equipment.
In 2016, in addition to the new stores, relamping with LED systems conti-
nued on the global network of existing stores, bringing the total propor-
tion of Hermès stores equipped with LED systems to 55%.
Air conditioning
Lower electricity consumption coupled with the fact that LED lighting
generates far less heat than traditional lighting has enabled us to consi-
der downsizing in-store air conditioning units.
This programme continued for all new store projects throughout 2016.
Thermal insulation
Particular attention is paid to insulating store façades (special glazing)
and industrial buildings (improved external insulation).
Other initiatives (installation of electricity consumption sub-meters and
motion detector systems in fitting rooms, washrooms and back offices)
were taken on all new store projects in 2016. These automated energy
consumption consolidation systems offer constant visibility allowing
rigorous management of energy use. Ever more efficient new technical
solutions are constantly being evaluated for progressive incorporation
into existing stores.
The choice of building materials, a reduction in their weight and an effort
to source supplies locally also improve results on the Bilan Carbone
®
assessments of new buildings and new stores.
2.5.6
Effective solutions for waste
management
The manufacturing units, with their technically different processes,
generate a wide diversity of pollutant releases: each industrial division
is focused on the dual objective of reducing pollutant releases and impro-
ving treatment to minimise its environmental footprint. This demands
continuousmonitoring as newprocesses or new technologies in this field
are invented every year.
Leather Goods
Leather goods production units represent limited sources of pollutant
releases, due to manufacturing procedures that are essentially manual
and respectful of the environment.
Air quality inside workshops is regularly analysed to ensure its quality.
Production sites have systematically replaced solvent-based adhesives
with water-based adhesives. Air conditioning, ventilation, heating, gluing
and sanding equipment that generate air emissions are fitted with filte-
ring devices that guarantee the quality of the air emitted.
Tanneries
Each tannery is equipped with an effluent treatment station and verifies
its industrial pollutant releases in compliance with the applicable stan-
dards. Regulatory inspection reports are submitted to the local autho-
rities on a regular basis. The division’s tanneries continually work on
improving the performance of effluent treatment.
In Montereau, the reduction of water consumption combined with the
production increase led toaconcentrationof pollutants in itswastewater.
In 2016, as in 2015, the site continued research on the sources of pollu-
tionand the implementationof complementary treatment. TheVivoin site
meanwhile continued its work to develop and secure the treatment of its
effluents, including the sludge system with the installation of a new filter