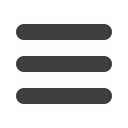

36
CHAPTER 2
THE PROCUREMENT PROCESS
the quantity of goods delivered to a location on a specific date. The bill of
lading details the number of boxes or containers delivered. (Other details
regarding the shipment appear on the packing slip and are the supplier’s
responsibility.) The bill of lading helps to ensure that the carrier is protected
against wrongful allegations that the carrier damaged, lost or otherwise
tampered with goods delivered.
• Discrepancy report:
A receiving discrepancy report will detail any
discrepancies on a shipment or shipments noted by the receiving department
of the buyer organisation. The procurement group or inventory management
personnel often become involved in following up on and resolving
discrepancies with the selling organisation.
Just-In-Time (JIT) manufacturing and purchasing systems allow firms to
eliminate most receiving documentation. Honda manufacturing, for example, has
eliminated the need for packing slips and inbound material inspection through
its JIT system [1].
2.3.6 EVALUATE SUPPLIER POST-PURCHASE PERFORMANCE
Once the product and/or service have been delivered, the supplier’s performance
must be evaluated to determine whether it has truly met the end user’s needs. A
firm needs to establish if the supplier has performed according to expectations
by using a formal supplier performance measurement system. If supplier
performance did not satisfy the user’s needs, the causes for this variance must
be identified and corrective action carried out.
Amajor decision to be made here is the frequency and nature of the evaluation.
It tends to vary by firm. However, there is general consensus amongst firms
that evaluation is necessary and should be carried out regularly, with feedback
on performance being provided to suppliers.
2.4 TYPES OF PURCHASES
Every organisation buys different types, or categories, of goods and services.
This section outlines the goods and services that an organisation typically
purchases.
2.4.1 RAW MATERIALS
This category would include items like crude oil, iron ore, copper, coal, lumber,
and so on. It can also include agricultural raw materials such as wheat, cotton
and corn. Typically, a raw material is characterised as a material where the
supplier has conducted little or no processing and it is purchased in its ‘raw’
state. Raw materials are often categorised according to a grade of material [1].