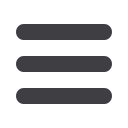

MADE TO MEASURE
1
2
W
hen it comes to 3D and
movies, most people would
immediately think of the
clunky glasses and the visual
images that appear to fly off the
screen towards you.
But there is another 3D revolution
underway and in its own quiet way,
it’s transforming the way films look
on screen. These days physical props
and costumes can be produced by
3D printers, and at the forefront of
this new production technique is
New Zealand company Weta
Workshop, whose most recent
project
Chappie
arrives this month
on DVD and Blu-ray.
Directed by sci-fi maestro Neill
Blomkamp, the film tells the story
of a police droid who develops
a mind of his own when he is
reprogrammed by his creator,
but inadvertently ends up in the
hands of some small-time crooks.
The task of bringing ‘Chappie’
– as he is dubbed by his new owners
– to life fell to visual effects giant
Image Engine and Weta, with the
two companies working together to
seamlessly blend the digital
and physical.
That’s where Lans Hansen comes
in. An industrial designer, he has run
Weta Workshop’s 3D department
for the past two years and has been
responsible for the department’s
increasing utilisation of 3D
printing technologies.
Hansen had previously worked with
Blomkamp on
Elysium
and
District 9
,
but with
Chappie
, the use of 3D printing
technology was taken to a whole
new level.
“We first started using 3D printing five or
six years ago,” Hansen explains to
STACK
from his Wellington office. “Back then it was
so expensive we would only print little bits
and pieces – for example, we might print the
scope of a gun. But when we got to
Chappie
,
there was nearly 200 parts that all had to
fit perfectly. We realised that 3D printing
was the only way we could pull this off. We
actually printed the entire robot – every single
part was printed and then molded. This was
a huge leap for us. The printed parts that
came out were extremely accurate and just
snapped together. It actually made the whole
process far more streamlined than if we had
used our previous techniques.”
Blomkamp came up with the original
design of Chappie, which Image Engine
then turned into a detailed digital model
that would be used for the animated
sequences. It was then up to Hansen and
his team to come up with a physical
representation of the robots;
a job which ultimately involved
creating 12 droids.
“There were different levels of
detail,” he says. “There were six ‘hero’
droids, and six background droids
– those are the ones you see in the
factory and being set on fire. But there
was also added complexity because as
Chappie goes through the movie, he
gets hit by poles, he gets set on fire,
spray-painted, etc. So we had to have
updates for the physical models to
reflect what is being animated.”
Like Chappie’s fictional creator,
Hansen is very proud of what the team
achieved in building the droids; for him,
it’s up there with the Green Goblin suit
he developed for
The Amazing Spider-
Man 2
– “that was incredibly complex,
because it had so many moving parts
and the stunt actors had to do back flips
wearing this suit” – another job which
required heavy use of 3D printers. And
Hansen has no doubt that the use of
the 3D printing technology is the way of
the future as far his job is concerned.
“I believe the next
Star Wars
film
in London is going to have a lot of
3D printing,” he says. “It seems it is
becoming a lot more commonplace. We
had one 3D printer five years ago, now I
have got 10 machines and they are
running almost 24 hours a day
at the moment. It is going to
become an integral part of the
process.”
There is another 3D
revolution underway and
in its own quiet way, it’s
transforming the way films
look on screen.
www.stack.net.au • Chappie is out on June 18