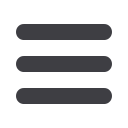

Chapter 7
– Inspection & Maintenance
7-4
Go to Chapter Start-
Table of Contents-
IndexC. Drive Belt
– The drive belt should be tight and in good condition.
Use a belt tension gauge to check tension (120 pounds maximum).
With experience, you can feel belt tension by twisting the belt. Try
feeling belt tension after using the gauge, when you know the
tension is correct. Replace belts if they are frayed or look worn.
If the clutch pulley/belt alignment is obviously off, you need to
loosen the compressor or mounting bracket, or both—and use the
alignment bar to line up the clutch pulley with the drive pulley.
Tighten compressor mounting bolts first, then the bolts holding the
bracket. The mounting bracket should have slots or other means of
adjustment to allow you to adjust the tension of the drive belt. When
you use a pry bar to apply tension, be sure you do not pry against the
compressor. Pry against the mounting bracket.
3. Check Hoses and Fittings
Check all hoses and fittings. Look for places where hoses flex when the
cab is tilted. Any places the hoses or fittings are fastened, clamped,
connected, bent or secured are potential wear points. This also applies to
places where hoses are not clamped or supported but should be (often
near the condenser). All of these spots are potential leak or damage
points. Tighten, re-fasten, add, or replace as indicated by your inspection.
4. Check for Refrigerant Leaks
System refrigerant leaks can be anywhere but there are obvious places.
You can spot some by looking for signs of refrigerant oil forced out with
refrigerant leakage. One location leaks frequently occur is the compressor
shaft seal. The shaft and seal are hidden behind the clutch assembly, but
centrifugal force will throw the oil off the shaft and against the engine,
bracket or whatever is close. Check these points when you examine the
compressor clutch and mounting bracket. A solution of soap and water
applied around potential leak points works well for detecting leaks. A leak
in the evaporator may be indicated if you feel around the condensate
drain hole and find oil present.
Note:
You can add inexpensive dry nitrogen gas to the sys-
tem instead of R-12 if system pressures are low. Dis-
pense the gas at no more than 200-250 PSI as this is
sufficient pressure to cause or indicate a leak point in
the AC system. AC service procedures for complete
system recovering of refrigerant, evacuating, and re-
charging are covered and illustrated in
Chapter 9.
Note:
A leaking heater core could also result in coolant at
the condensate drain.