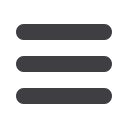

Ionisers take static out of manufacturing environments
Static is problematic in themanufacturing environment. Static causes dust and this in return comes
with its own set of problems. From dealing with the nuisance of products clinging to each other,
plastic sheets not separating property to managing possible damage to electrical products.There
is also the real hazard of a possible fire which can be caused by a spark in a chemically sensi-
tive environment.
SMC Pneumatics
is able to offer a solution to these ‘every day’ manufacturing
problems by means of the three different types of ionisers available from their product range.
“When working with plastics you often have an unwanted but unavoidable charge of electric-
ity” explains Brian Abbott, Product Manager Pneumatics at SMC. According to Abbott, there are
various options of ionisers available depending on the application and the environment. “The
bar type is equipped with nozzles which generates charge and air then blows the charge onto
the application.This could work in a PET environment for example. It would also be suitable for
lamination and web printing.The bar type varies in length and performance options.The nozzles
can be equipped with condition monitoring and therefore easy maintenance and replacement of
the nozzles are not a problem.The unique thing about the SMC ioniser is that it can be ordered
in a variant which is equipped with a sensor.The sensor has a feedback device which is able to
determine if a positive or negative charge is required, and then it will generate accordingly.The
charge relates back to a voltage so that the unit can measure the charge.This is communicated
back to ioniser and ioniser will generate ions to balance out the charge.
An option without a sensor is also available. In this case the unit will generate alternate charge
which ‘bombards’ the application with positive and negative ions until it neutralisers the ap-
plication.This would however be a less
energy efficient option.
Enquiries: Email sales@smcpneumatics.
co.zaor visit
www.smcworld.comControl system for Europe’s first hybrid-flywheel energy
storage plant
Yokogawa
Ireland has delivered a control system for Europe’s first hybrid energy storage plant in
Rhode, County Offaly, Ireland.The hybrid energy storage plant was officially launched and opened
in early November 2015 by Schwungrad Energie, the owner and operator of the facility. Schwungrad
Energie has developed this hybrid power storage system in collaboration with the Department of
Physics and Energy at the University of Limerick, and will work with the Irish transmissions system
operator to connect the plant to the power grid as a demonstration project under its Smart Grid
Programme.The Rhode hybrid demo project comprises of two Beacon Power 160 kWflywheels and
Hitachi Chemical valve regulated lead acid batteries of up to 240 kW.The plant will have a maximum
import capacity of 400 kVA andmaximumexport capacity of 422 kVAwhen completed.The flywheel
system, with very high cycling ability, can rapidly absorb short-termexcess grid energy and generate
energy as needed by grid operators. Batteries can provide energy over longer durations but have
more limited cycling capabilities.The hybrid flywheel will assist in disruptionmitigation, during times
of unexpected demand or sudden changes in energy supply and demand. After the completion of
construction, the plant will enter a test operation phase fromFebruary 2016.The Schwungrad Energie
plant will be the first field test of a hybrid-flywheel energy storage system in Europe.
Enquiries: Christie Cronje.Tel. 011 831 6300 or
or visit
www.yokogawa.com/zaROUND UP
CONTROL SYSTEMS + AUTOMATION
15
January ‘16
Electricity+Control