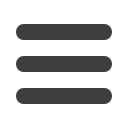

BUSINESS OVERVIEW
06
6.4 Operations
SPOT AND LONG-TERM SWU PRICES FROM 2005 TO 2015
(IN CURRENT US DOLLARS)
Spot SWU
LT SWU
US
Source: UxC.
180
160
140
120
60
40
20
0
80
100
Jan. 05
Jan. 06
Jan. 07
Jan. 08
Jan. 09
Jan. 10
Jan. 11
Jan. 12
Jan. 14
Jan. 16
Dec. 16
Jan. 15
Jan. 13
Outlook and development goals
One of the strategic objectives for the operations in the front end of the cycle is to
strengthen AREVA’s position as a major player in the global conversion market. It
will continue to benefit from the integration of the group’s Front End operations
and its physical proximity to Europe’s enrichment plants.
To achieve this goal, AREVA decided in 2007 to replace its uranium conversion
production capabilities by investing in a new conversion plant at the Malvési and
Tricastin sites; this is known as the Comurhex II project. The new plant will have
a full production capacity of 15,000 metric tons, with the possibility of increasing
capacity later to 21,000 metric tons if, and only if, market conditions permit. At this
point, Comurhex II is the only new conversion plant project to be launched in the
world. It will replace the existing capacity of Comurhex I. The Comurhex II plant
is designed to offer maximum security of supply to our customers. In addition, it
meets themost recent safety standards, particularly in terms of its ability to withstand
earthquakes and flooding. Comurhex II also received triple ISO 9001, ISO 14001
and OHSAS 18001 certification. Recently, the plant demonstrated its energy
efficiency innovations when it received ISO 50001 certification for using the heat
produced by electrolysis to heat the buildings.
With Comurhex II, the environmental footprint will decrease considerably:
p
75% reduction in ammonia releases, 50% reduction in nitric acid and fluorine,
and 60% reduction in potassium hydroxide, thanks to the Isoflash process;
p
90% reduction in the annual consumption of water.
The Comurhex II project continued in 2016:
p
at the Malvési site with the continued ramp-up of industrial production following
the qualification of the UF
4
produced by the new thermal denitration process,
which replaced chemical denitration;
p
at the Tricastin site, with the continued construction of the fluorination, effluent
treatment and utilities functions. The fluorination building entered the testing
phase in the early autumn.
In 2015, the nuclear safety authority ASN approved AREVA’s request to extend the
operation of the Comurhex I production plant until the end of 2017. This will reduce
the duration of the non-production phase, with integrated startup of Comurhex II at
both sites slated for the end of 2018.
The backlog in the enrichment business offers more than 10 years of visibility. Given
the known operating period of current reactors, the conversion and enrichment
markets should see growth in volume by 2030. The sharp upturn in demand in
Asia should largely offset a decline in demand in Europe.
The Georges Besse II plant reached full production capacity at the end of 2016,
strengthening the return on investment for the future through implementation of
operational and commercial levers.
6.4.1.3.
BACK END
NewCo’s Back End operations combine the recycling, nuclear logistics, dismantling
and services, and waste management operations.
Key figures
2016
2015
Revenue*
(in millions of euros)
1,523
1,593
Operating income
(in millions of euros)
65
(184)
Workforce at year end**
10,941
11,050
* Contribution to consolidated revenue.
** Workforce consistent with the breakdown by operation shown in Chapter 17,
Employees.
6.4.1.3.1.
Recycling
Businesses
The Recycling business uses processes allowing its customers to recycle used
fuel into fresh fuel and to package final waste in standardized containers in a safe
and stable manner.
The Recycling business earns a return internationally on the technical and industrial
expertise developed in its facilities and the know-how acquired by the Dismantling
and Services business at the sites of the group and of its French customers. In
particular, it designs and builds new recycling plants in the framework of international
partnerships with countries seeking to acquire their own production plants.
After nuclear fuel has been used in a light water reactor, 95 to 96% of its content
is material that is still recyclable: 1% is plutonium and 94 to 95% is uranium.
The first step in fuel recycling is to separate these reusable materials from the
final waste. The latter is packaged in “universal waste canisters” for safe storage
and transportation. This package is designed for high integrity and containment
performance for purposes of geologic disposal. Following the treatment stage, the
reusable materials are recovered for recycling. Depending on the utility’s strategy,
the recycled, re-enriched uranium from used fuel treatment, also called RepU, may
be recycled in the form of enriched recycled uranium fuel (ERU), or stored in stable
form, constituting a uranium stockpile. The plutonium is used to fabricate another
type of fuel, MOX, of which AREVA is the world’s leading producer.
2016 AREVA
REFERENCE DOCUMENT
73