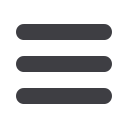

40
M
ay
2016
T E CHNOLOG Y
Easy cleaning of tubes and hoses
STAUFF Clean offers a simple option
for removing unwanted contamination
in tubes and hoses for maintenance
purposes. In addition, the system can
be an alternative to time-consuming
flushing processes during the production
and processing of tubes and hoses.
Stauff states that its system offers time
and cost benefits compared to traditional
cleaning methods. Stauff Clean
essentially consists of a lightweight,
ergonomically shaped compressed air
gun, supplied with sufficient compressed
air via a quick release coupling, and a
range of specially shaped plastic nozzles
that are connected to the handheld tool
with retaining rings. The system requires
compressed air at approximately 6 to
8 bar. The compressed air gun is used
to accelerate foam projectiles into the
tube or hose to be cleaned. The plastic
nozzles compress the inserted projectile,
and also ensure that the connection is
as airtight as possible, while creating a
smooth transition into the tube or hose.
This method is safe and environmentally
friendly, and the operation is intuitive and
quickly learned.
The foam projectiles that carry out
the cleaning are 15 per cent larger than
the inner diameter of the tube or hose
to be cleaned. This creates friction that
effectively releases contaminations.
In addition to a universal version
that covers inner diameters between 6
and 60mm, numerous other projectile
versions with different textures and
grain sizes are available, eg for
removing traces of rust and other coarse
contaminations. The system can be used
up to a tube/hose length of 100m, and
regardless of any installed couplings,
fittings and valves. For more than 50
years, the Stauff Group has developed,
manufactured and distributed pipework
equipment and hydraulic components for
mechanical and plant engineering.
Walter Stauffenberg GmbH & Co KG
– Germany
Email:
sales@stauff.comWebsite:
www.stauff.comStauff Clean is supplied as a complete set
in a convenient case, on request
Equipping the compressed air gun with a
foam projectile
SIDE LOADING FOR FAST TOOL
CHANGE AND NO LIFTING REQUIRED
• Infinitely adjustable
expansion & reduction
• High production
capability
• Up to Ø 152mm
• No tube clamping
required
• End form on or
near bends
• High quality build with
practical platforms
• Full 12 month warranty.
• Twin Head Machines
also available
Unit 24, Padgets Lane, South Moons Moat,
Redditch, Worcestershire B98 0RB, England.
T: +44 (0)1527 518520 E:
info@avamatic.co.ukW:
www.avamatic.co.ukGermany: Tel: 02150 2500
Netherlands/Belgium: Tel: (04756) 6888 USA: Tel: 708 272 7880
TUBE END FORMING
AV65