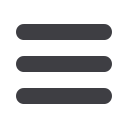

May 2016
21
www.read-eurowire.comCorporate
News
Corporate
Decalub green cleaning
TecHnOlOgieS FOcuS On:
DECALUB
31, avenue de Condé
77500 CHELLES, FRANCE
E-mail:
info@decalub.comWebsite:
www.decalub.comWire Cleaning
( for plating and high glossy finish )
Wire Rod Lubrication
( for frictionless drawing )
Rod Dry Preparation
( with no speed limit )
▲
The new purpose-built Class 7 clean room at William Hughes’ UK headquarters
Clean bill of health
SINCE William Hughes, a specialist
manufacturer of springs and wire
components, acquired AC Services
in the summer of 2015, the company
has been busy establishing an 80m²
high-specification clean room at its
Stalbridge, Dorset, UK, headquarters.
Rated at Class 7 in accordance with ISo
14644-1, this advanced sub-contract
facility is now open. It is already being
used by some of the best-known
manufacturers in sectors such as
aerospace and hydraulics for the cleaning
of small batch, precision machined and
fabricated parts to meticulous standards.
“From the outset we wanted to create
a facility featuring the latest, modular
clean room technologies and furniture,”
said special processes manager Shaun
tattershall. “We have adopted the
previous solvent and aqueous cleaning
systems – both of which offer ultrasonic
capability – used by AC Services, but
pretty much everything else is new.”
this
includes
high-grade
stainless
steel furniture that is designed to help
minimise particulate levels. What is more,
the open plan clean room has been
designed for optimum product flow
based on the latest lean manufacturing
methodologies.
It will thus prove ideal for any company
looking to sub-contract its cleaning
requirements, not just from the aerospace
and hydraulics industries, but also
defence, nuclear, medical, electronics and
oil and gas.
the new clean room, which incorporates
an inspection dark room so that parts
can be viewed under ultra-violet light, is
already being used for oxygen-related
cleaning applications, predominantly for
aerospace giant Honeywell.
typically, these comprise high-precision
machined components, springs and other
parts that go into oxygen equipment
such as breathing apparatus, facemasks
and ducting. these parts, some of which
are also used in liquid oxygen (loX)
systems, are cleaned using approved
cleaning solvents and solutions.
“the existing class room specification
for these products is ISo Class 8, so our
ISo Class 7 facility is more than suitable
– it’s the equivalent of a Class 10,000
cleanroom using the Federal Standard
209E,” added Mr tattershall.
It is also worth noting that William
Hughes can offer in-house cleaning
verification capabilities. Here, samples
are taken from batches that have been
cleaned. the samples are rinsed with
filtered, deionised water over a 0.45µm
filter membrane.
Any particulates captured are both
counted
and
examined
under
a
microscope. As a result, customers are
assured that their components will
always meet the specified particulate
count.
this confidence is vital, as a contaminated
system component/assembly could result
in a chemical reaction, an explosion and/
or a total system or device failure.
“We take the utmost care with customer
parts and ensure that all cleaning is
compatible with the component being
processed,” added Mr tattershall. “Cleaned
items are placed into hermetically sealed
bags that will not be opened again until
required for further processing, such as
assembly.”
the solvent and aqueous cleaning
systems within the new facility at William
Hughes can accommodate precision parts
up to 300 by 200mm in size. Along with
metallic parts, materials such as rubbers
or plastics (or a combination of these with
metal) can also be cleaned.
William Hughes Ltd – UK
Website
:
www.wmhughes.co.uk