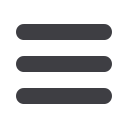

News
Technology
May 2016
36
www.read-eurowire.comDeWAL Industries has introduced a new line of high
temperature, silicone-free adhesive tapes for the aerospace
composite industry.
The tapes are suitable for low out-gassing applications requiring
EMS 595. The group includes a woven glass tape, a foil/glass
laminate tape, a red polyester tape and high density PTFE.
It is becoming an ever-increasing problem in sensitive
manufacturing processes to introduce silicone elements. DeWAL
has addressed this issue by formulating the most popular tapes
in versions which contain no silicone. While suitable for the
aerospace composite industry, they are additionally used in
automotive and electronic applications where silicone can also
be of concern.
DeWAL’s new polyester tapes for composite lay-up are DW 915-1
and DW915-2. They are 100 per cent silicone-free, offering a high
temperature, high bond, clean release acrylic adhesive. Both
pass the ASTM E595 low out-gassing test for no out-gassing
contamination
They use a 1mm film and 2mm film, respectively, and both are
very conformable.
DeWAL’s PTFE tape for use as composite tool coat is DW716-2HD.
The printable glass tape DW379 is used in aerospace blanket
seaming and also as a wire harness and transformer wrap.
The fourth tape in this new series, DW417, is a flexible dead soft
foil supplied on a release liner. The aluminium laminate makes it
an ideal heat shield tape.
As with the polyester tapes, the other three tapes also pass the EMS
595 requirement and offer low out-gassing, silicone-free operation.
DeWAL Industries – USA
Website
:
www.dewal.comOriginally developed for the food
industries, the Uhing-easylock® clamping
system has long since found its way into
other sectors as well. It is sought after
for production processes using winders
or coilers or where safe and efficient
clamping or locking is essential.
A
classical
application
for
the
Uhing-easylock are the processes in
the wire and cable industries where the
torque transfer the clamping system
provides is of particular importance.
The axially displaceable Uhing-easylock
features a clamping ring that, when
subjected to axial tensioning forces,
tilts on the shaft and engages with it.
The locking effect is proportional to the
tensioning force.
In
packaging
technology,
the
Uhing-easylock holds and locks roll cores
of foils and other material, and it is also
used to quickly adjust material guides. As
operating the clamping module does not
require any tools, the work environment
remains free of utensils such as wrenches.
Changing the clamping module occurs
quickly and easily with only one hand.
The
vibration
proofness
of
the
Uhing-easylock clamping module is a key
feature in static applications where high
locking forces are required, for example in
screening machines.
Once again, the module convinces by
its easy and effective handling. It can be
unlocked quickly with only one hand and
mounted in a very short time after a screen
change, and screening can continue.
A special positive release add-on module
was developed for the Uhing-easylock
fast clamping system. It makes changing
filled spools easier if the clamping disc
should fail to unlock. This can happen
if a residual force still acts against the
tensioning wheel although it was fully
turned back.
A residual force may remain if, for
example, a spool still rests on the pintle
after unclamping, or if the spool has
expanded during winding. As a result,
the locking ring may fail to return to its
perpendicular position, which makes
unlocking difficult or totally impossible.
The positive release becomes effective
when the clamping wheel is turned to its
rear limit position, which is done with one
hand only.
“The compact Uhing-easylock® clamping
module features an axially symmetric,
modular design,” said Jörg Wadehn, Uhing
technical director. “In this way, it can
be easily adapted to suit the respective
clamping task. The simple transmission of
braking moments to the roll or spool also
translates to a high degree of safety in
case an emergency stop is needed.”
The lightweight, ergonomically designed
clamping
module
generating
high
locking forces on a plain shaft is suited
for static applications but also for driven
shafts with unmachined surfaces.
It comes in ten different sizes for shaft
diameters between 10 and 40mm; the
clamping module with integrated positive
release is available for shaft diameters
between 25 and 40mm. The required
surface hardness of the shaft is at least 55
HRC for a surface roughness Ra of 0.2-0.4
µm.
Joachim Uhing GmbH & Co KG –
Germany
Website
:
www.uhing.comNew tapes for the aerospace composite industry
Versatile easylock fast clamping system
▲
▲
The easylock EL10 from Uhing