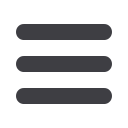

10
S
eptember
2011
www.read-tpt.com›
I
ndustry
N
ews
Hot wire
welding
demo tour
THE Polysoude hot wire welding demo
tour has travelled around Europe, and
completed many of the 30 demonstrations
planned worldwide. The company reports
that the interest of participants in the event
has so far been high.
The tour started in Nantes, France
(Polysoude’s headquarters), then visited
the UK, where TWI hosted the event at
its premises in Cambridge and also
in Rotherham, to demonstrate the latest
development in the TIG hot wire process.
Equipment presented during several live
demonstrations included P6 HW hot wire
power source; Polycar 60 PLC hot wire
carriage welding head; and MU IV 195 HW
hot wire open type ‘grip-it’ welding head.
The UK event hosted over 40 visitors who
were representing around 15 companies, all
of which are specialists in various applications
in welding and cladding solutions.
Visitors were particularly interested
in applications for the nuclear and
petrochemical industries, and were keen
to know more about Polysoude’s ability
to provide specialised welding solutions
in these fields. After one week in the
UK, the demo tour returned to France,
at the Welding Institute in Port de Bouc,
near to Marseille. Nearly one hundred
specialists, coming from markets such
as nuclear, petrochemical and pipework
fabrication, were impressed by the increase
in productivity without loss in quality shown
by the new Polysoude equipment compared
to manual process or the conventional TIG
cold wire process.
The worldwide tour continued travelling
through Norway, and was scheduled to
cross Germany, Austria, Slovakia, Italy and
Switzerland before the summer holidays.
The final tour will be in the USA and in Japan
in the autumn.
Polysoude SAS
– France
Fax: +33 2 40 68 11 88
Website:
www.polysoude.comRAFTER Equipment Corporation has
successfully replaced a raft set on a
competitor’s tube mill. The customer came
to the company looking to replace the
original rafts (both primary and spare sets)
because they were no longer able to make
quality tubing consistently and efficiently.
The project was complicated by the
use of a custom raft exchange system
and the lack of any engineering details.
Rafter had to rely mainly on measurements
obtained on-site. In addition to replacing
the rafts, the customer decided to remove
the original third-stand style drive shaft
disconnect system and original automatic
top-shaft positioning system, both of
which had failed to live up to expectations.
Rafter assisted with this conversion by
supplying new universal drive shafts with
quick-disconnect couplings. The customer
installed the new raft sets over a weekend
shutdown, and was back in production
on Monday morning. Rafter Equipment
Corporation manufactures tube and
pipe mills, roll forming machines, cut-
off machines, auxiliary and other related
tube and pipe mill machinery. Additional
services include rebuilding and upgrading
mill equipment.
Rafter Equipment Corporation
– USA
Fax: +1 440 572 3703
Website:
www.rafterequipment.comRafter replaces raft set on competitor’s mill
P6 hot wire
power source
Polycar MU IV 195 HW hot wire open type
welding head
Live demonstrations in France