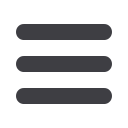

S
eptember
2011
131
›
W
elding
E
quipment
Giant welding project in
Bosnia Herzegovina
IN Zeljusa, about 10Km from Mostar, Bosnia
Herzegovina – scene of terrible fighting
during the war of the 1990s – an ambitious
project is about to be completed: a state-
of-the-art irrigation system built on a 300
hectare vineyard.
The carrying out of such an irrigation
system entails the use of 45km of HDPE
tube, divided into the main duct and the
junctions.
The main duct is made of Ø250mm
plastic pipes, SDR 17; the junctions,
respectively: 15km of Ø125mm pipe, SDR
26 PN6; 15km of 110mm Ø pipe, SDR 26
PN6; and 15km of Ø90mm, SDR 26 PN6
to finally end with a sophisticated drop-by-
drop irrigation system made of decoders
connected with a central programmer.
For the welding, the local firm Procedo,
supported by the experience of PlusPipe Srl,
has chosen the Italian technology of Ritmo
SpA. In particular, two butt fusion welders
of the Basic Line: Basic 160 (working range
from 40 to 160mm) and Basic 250 (working
range from 75 to 250mm), both supplied with
adapters. The third machine involved is Elektra
400, an electrofusion welding machine.
The Basic machines were responsible
for the main ducts welding, while Elektra
400 had to finalise the joining of the pipes
connecting to the drop-by-drop system.
The environment – 300 hectares of
construction site that requires constant
movement – brought out the best
characteristics of the Basic machines:
robustness and manoeuvrability, reliability
and precision. In particular, two are the
features esteemed by the operators. The first
one regards the electronic thermo-regulator
Digital Dragon that guarantees a precise
control of the heating plate’s temperature
and is very easy to read and set up. The
other preferred feature is the SMARTLock
adapters system (Ritmo patent) that allows
the setting up of a new working range of
the welder’s clamp in a very short time, a
substantial time-saving for all operators.
The Elektra 400 is very reliable – it can
weld couplings from Ø20 to 400mm, offering
something that welders really appreciate:
the machine can work continuously, with
no cooling time, under 40°C. Furthermore,
thanks to a scanner-reading system that
allows the automatic setting of welding
parameters and a memory able to record
up to 4,000 welding cycles, Elektra 400
has highlighted its qualities inside the
construction site. While the welding
presented no issues, the extremely rocky
soil of the site forced the operators to overfill
the bed where the pipes will be placed,
handling the duct with utmost care.
Ritmo SpA
– Italy
Email:
info@ritmo.itWebsite:
www.ritmo.it