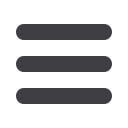

WCN
Issue N° 44
www.iwma.org24
As mentioned before, drawing line
speeds are increasing and thus
we must turn our attention to wire
lubrication in order to provide sufficient
amount of emulsion at an adequate
temperature and pressure at each
critical point of the line.
The importance of final die spraying is
often underestimated.
At the final die the wire reaches its
minimum diameter and the wire speed
is the highest within the line. Due to
the fact that the final die is located last
in the drawing lubricant supply line,
neither the pressure nor the quantity of
the emulsion are adequate for proper
lubrication and rinsing of the final die.
For a sufficient grade of lubrication
here, a separate line from the lubricant
supply system with adjustable spraying
is absolutely crucial.
The increasing demand for reduced
cross section reduction on the fine
wire drawing lines requires an increase
in the number of drafts. A high number
of drafts in gearbox machines results
in high cumulative slip towards the
wire inlet side of the line.
High slip has a negative effect on
the lifetime of the drawing capstans,
on the quality of plated wires, on the
noise level of the lines and on the
frequency of wire breaks. Drawing
machines with three drives reduce
the slip at the passages to about 5%
and the maximum slip at the wire inlet
of standard lines from around 45% to
15%.
Power splitting from two to three
motors results in the reduced
performance of the single motors
which makes the application of AC
drives cheaper – another advantage
of this concept. The advantage arising
from the application of AC drive
technology is self-explanatory.
Annealing
Up-to-date multiwire annealers have
to treat multiple wires individually
but equally throughout the annealing
path to ensure equal electrical and
physical properties of the wires for the
downstream processes. They must be
simply made ‘Triple A’ − Advanced,
Accessible and Adjustable and, of
course, attractive in price.
The market offers machines with
various annealing principles. 2-zone
annealers with preheating and main
annealing zone or 3-zone annealers
Lubrication of drawing
materials
- Control of flow rate
- Control of temperature
- Spraying of capstans and dies
- Cleaning of lubricant
- Separate lubricant supply for
final die holders
Drawing lubricant supply
Fine die holder
Drive concept
Slip reduction for long wire drawing machines
Slip reduction by using 3-motor technique
- Less abrasion of tin and nickel
- Less wear of drawing capstans
- Reduced noise
- Smaller motor sizes, AC-technique becomes more reasonable
3.2 Annealing
Triple A
Advanced
Accessible
Adjustable
and
Attractive
in price
3-Zone annealing
• Higher energy consumption
• Better drying due to reheating
zone
• Diameter range < 0.25mm
K2 (+)
K3 (-)
K1/K4
2-Zone annealing
• Less energy consumption
• Higher efficiency
• Diameter range > 0.25mm
K2 (+)
K1 (-)
K3 (-)