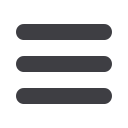

Tube mi l ls and rol l forming
www.read-tpt.comS
eptember
2013
113
Casting thin-walled Cu-DHP tubes
UPCAST upward continuous casting
technology is best known for the
production of Cu-OF rod used within the
wire and cable industry. With the advent
of Upcast SGTube, the technology has
been applied to the casting of thin-
walled Cu-DHP tubes. Cast tubes with a
fine grain structure come in heavy coils
straight from the casting line ready for
drawing.
The baseline Upcast technology is
characterised by low lifecycle costs, easy
variation of output, upgradability and
small environmental footprint. SGTube
brings all these benefits to the disposal
of copper tube manufacturers, while at
the same time replacing many costly
production stages in existing tube mills.
Casting of copper tubes has been
possible with the Upcast system from
the very start. However, if the cast grain
structure is too coarse the tube cannot
be successfully drawn, which limits its
use to the manufacture of tube fittings.
A few years ago, Upcast embarked on
an R&D project to reduce the size of the
cast grains, in order to overcome this
restriction. The result was the SGTube
technology.
To exploit the full potential of SGTube,
Upcast has joined forces with Asmag
GmbH to develop a new concept called
Cast&Draw, for cost-efficient production
of copper tubes. The ‘cast’ portion
consists of the SGTube process while the
‘Draw’ part includes straight drawing and
intermediate annealing equipment. The
tube produced is a semi-product that can
then be further processed with standard
spinner blocks and finishing equipment
into various final tube products. Upcast
states that the main advantage gained
when taking the Cast&Draw production
route is the savings in overall costs due
to the cast tube being close to final tube
product sizes.
In more traditional production
methods, several costly steps are
required to reach the same point. A
Cast&Draw production line also requires
less space than conventional equipment.
Output from a single Cast&Draw unit is
up to 12,000tpa.
The first tube mill with its production
based onCast&Drawhas been operating
for more than two years. Two follow-on
SGTube lines, which are ‘hybrid’ units
capable of producing both rod and tube,
were brought online earlier this year.
Hybridity offers a solution for companies
with a diverse product range but low
product-specific volumes. Next year
will see the first delivery of a greenfield
Cast&Draw plant.
Cast&Draw is currently being used in
the production of sanitary and certain
ACR tubing, with a gradual shift to more
demanding products. Adaption of the
Cast&Draw concept to copper alloys
is also near, one example being Cu-Ni
tubes for seawater applications.
Upcast Oy
– Finland
Fax: +358 207 577 401
Email:
sales@upcast.comWebsite:
www.upcast.comUpcast SGTube
casting technology
WH-350 reshaping stands
YODER Manufacturing of Cleveland,
Ohio, a member of the Formtek Group,
has recently been contracted to refurbish
and upgrade an existing WH-350 tube
mill to produce structural shapes (HSS).
Formtek has designed a new style
reshaping stand that enables the
operator to adjust the inboard, or drive
side, side cluster from the operator side
of the mill, which eliminates the need for
the operator to enter a dangerous area
of the tube mill for simple adjustments.
The reshaping stand has single point
top shaft adjustment and individual side
cluster adjustment to allow the operator
to fine tune the setup to get the desired
shape.
In most cases, the reshaping portion
of the sizing or calibration machine
consists of two or three reshaping stands
coupled after two or three “round” drive
stands.
This configuration yields enough
distance to properly “move” material
to minimise marking from tooling while
providing the proper amount of drive
power necessary for reshaping wall
thicknesses up to 0.25" (6.4mm).
The system will be capable of
reshaping up to 4" (101.6mm) square
or up to 2" x 6" (50.8 x 152.4mm)
rectangles.
Formtek is a group of long-established
companies, each with a well-known
name and a history of providing
innovative, reliable equipment to the
metal forming and metal processing
industries. As a single source provider,
Formtek continues to supply its
customers with the highest quality
equipment, parts and service available
in the industries it serves.
Formtek
– USA
Website
www.formtekgroup.com