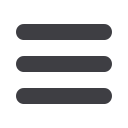

Technology News
www.read-tpt.com66
S
eptember
2013
The best draw tooling
IN tube drawing, the key to producing
the finest quality tube starts with having
the proper draw tooling. Draw tooling is
the heart of the process. Without proper
tooling, tool life, productivity and profit
margins may all be compromised.
Glen Carbide focuses on the grade
of carbide, tooling design and tooling
quality as the essential elements in
making the ideal draw tooling for each
unique application. Tube drawing is
accomplished in the die box on a draw
block or drawbench, where the draw tools
work in conjunction with a lubricant in
effort to affect change on the tube – most
notably, the surface finish, the outside
dimensions, the wall thickness and the
length of the tube. The draw tooling in the
die box is comprised typically of carbide
dies, plugs and mandrels.
As a tool maker, Glencarbide first
looks at utilising the proper grade of
carbide for the application. Different
metals respond differently to each set
of tools. Soft metals such as copper
and aluminium can be drawn using
harder grades of carbide, whereas
hard metals such as steel and stainless
steel work better with tougher grades
of carbide. The objective is to find the
grade of carbide that works best for
your application. It is important to find
a grade that is tough enough that it
will not break, but hard enough to last
as long as possible. With more than
50 years of experience the company
has developed a good feel for what
performs the best in most tube drawing
applications.
The design of the draw tooling may
be the most important of the three
elements. The key is to provide suitable
tool geometries that will promote proper
lubrication, which in turn will help
provide better tool life, longer production
runs and superior quality tubing.
When designing the draw tooling,
Glencarbide works with the customer
to determine the shape and dimension
of the incoming tube and develop a die
design that will transition the tube from
either a round to round, round to shape
or shape to shape finished product. Each
die is custom designed to transition the
metal into its final shape, accounting for
stresses unique to that shape.
When designing the geometry of the
draw plug, it is vital to keep in mind the
lubrication flow. There must be a gap
between the inside diameter of the tube
and the major diameter of the plug. The
gap will allow the lubricant to pass into
the transition angle and be drawn into
the bearing land of the plug. This will
provide a thin film barrier for the plug.
Direct contact will damage the carbide
tooling, which in turn will scratch the
walls of the tube.
The transition angle of the plug is also
critical. It must work in conjunction with
the die angle to create a wedge that will
effectively control the wall thickness as
the tube is being drawn. An effective
wedge will help minimise the draw force
required to form the tube. A mandrel is
often used in drawing round to shape or
shape to shape tube.
Glencarbide
– USA
Website:
www.glencarbide.com