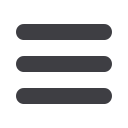

Mechanical Technology — July 2016
17
⎪
Power transmission, bearings, bushes and seals
⎪
“
R
oot cause analysis is a
process for identifying
the true underlying cause
of a particular failure and
using that information to allow for cor-
rective or preventative action,” says
P rez-Sánchez.
The process commences with a criti-
cal data-collection phase, followed by an
analysis and concluding with the imple-
mentation of a solution. Data collection
is initiated by BI’s customers, with BI
sales staff tasked with collating as much
information about the customer and the
particular application as possible.
“A general schematic of the applica-
tion can give a lot of insight into any
problems and potential solutions. This
information is critical for the compila-
tion of an accurate root cause analysis
report,” he advises.
Bearings International (BI) is establishing itself as a technical partner
to industry with an array of value-added services on offer, including
bearing root cause failure analysis. BI engineering manager, Josu
P rez-Sánchez, explains.
BI brands showcased
at NAMPO 2016
F
rom bearings and transmission com-
ponents to power tools and hand
cleaners, leading supplier Bearings
International (BI) displayed a slew of its top
international brands at Grain SA’s NAMPO
Harvest Day, which was held from May 17
to 20, 2016 in Bothaville in the Free State.
Billed as one of the largest privately-
organised and owned exhibitions of its
kind in the world, BI marketing manager
Gugulethu Nkutha says the event provided
an ideal opportunity for the company to
showcase its product and service offering
to the agricultural sector.
BI’s diverse product line-up meets a
broad spectrum of requirements of the
South African agricultural sector. This
runs the gamut from supplying bearings
and chain to couplings and transmission
products for arduous farming applications
such as ploughing, planting, harvesting
and baling.
BI is also able to provide expert advice
on keeping farming equipment operating at
optimum efficiency, in addition to outlining
the most optimal maintenance procedures.
It carries a comprehensive stockholding
of spares, in addition to chain and V-belt
drives.
“We work together with our customers,
with the understanding that the current eco-
nomic environment places more pressure
on them to do more with less – together
we ensure they grow, while we grow,”
Nkutha says.
A highlight of BI’s participation at this
year’s event was the presence of a dedi-
cated sales team and product managers to
answer all customer queries and to provide
comprehensive information on the brands
represented.
Top international brands showcased
included KML (bearings and transmission
components), Loctite (adhesives, sealants
and surface treatment), FAG (special-
ist bearings), Citronol (hand cleaners),
Makita (power tools), Rocol (lubricants),
Dodge (housed bearings), KML, Agri
Chain, TR Gearboxes, Jonnesway and Opti/
Goodyear.
q
Bearing root-cause failure
analysis service
BI showcased its diverse product and service offering to the agricultural sector at NAMPO 2016
held in the Free State town of Bothaville.
“The process also allows for interac-
tion and the opportunity to get to know
our customers’ challenges and specific
needs better,” P rez-Sánchez continues.
The data-gathering process may also
involve an engineering representative
visiting the plant to provide holistic
insights into that customer’s specific
requirements.
The information gathered is then
tabulated into an inspection report sub-
mitted to the BI engineering department,
where the product in question is cleaned
and disassembled in order to carry out a
proper forensic investigation.
The solution phase encompasses
compiling the actual root cause analy-
sis report, which includes a thorough
description of the damage incurred, the
primary reason for this damage, and
any contributing factors for the failure.
The report also includes a conclusion
and detailed recommendations – and it
is presented to the customer in person.
“From a warranty standpoint, we
offer the service in order to help us
determine whether or not our customers
are entitled to a claim,” P rez-Sánchez
elaborates. This service also plays a key
role in customers’ production improve-
ment programmes, as the information
provided allows for continual plant reli-
ability improvement.
“We strongly believe we should rather
compete on value, providing advanced,
industry-specific solutions and services,
thus safeguarding industry sustainabil-
ity,” adds Burtie Roberts, CEO of BI.
BI, part of the Hudaco Group, has
consolidated its position as a leading
distributor of bearings and power trans-
mission products in Southern Africa by
launching a new brand identity at the
end of last year. “Our aim is to become
a proactive company providing excel-
lent service to our customers to ensure
we are the preferred supplier,” Roberts
concludes.
q