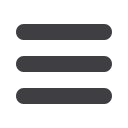

new products
78 l New-Tech Magazine
New Cadence Modus Test
Solution Delivers Up to 3X
Reduction in SoC Test Time
Physically aware 2D Elastic
Compression architecture reduces
test logic wirelength by up to 2.6X
and enables compression ratios
to scale beyond 400X without
impacting design size
Cadence Design Systems, Inc.
(NASDAQ: CDNS) todayannounced
the new Modus™ Test Solution
that enables design engineers to
achieve an up to 3X reduction in test
time, thereby reducing production
test cost and increasing silicon
profit margins. This next-generation
test solution incorporates patent-
pending, physically aware 2D
Elastic Compression architecture
that enables compression ratios
beyond 400X without impacting
design size or routing.
To address the challenges that come
with testing designs, the Cadence®
Modus Test Solution includes the
following innovative capabilities:
2D compression: Scan compression
logic forms a physically aware
two-dimensional
grid
across
the chip floorplan, enabling
higher compression ratios with
reduced wirelength. At 100X
compression ratios, wirelength for
2D compression can be up to 2.6X
smaller than current industry scan
compression architectures.
Elastic compression: Registers
embedded in the decompression
logic enable fault coverage to be
maintained at compression ratios
beyond 400X by controlling care
bits sequentially across multiple
scan cycles during automatic test
pattern generation (ATPG).
Embedded memory bus support:
A shared test access bus can
be inserted to perform at-speed
programmable memory built-in
self test (PMBIST) across multiple
embedded memories in an IP
core. New soft programmable test
algorithms for FinFET SRAMs and
automotive safety applications are
also included with this feature.
Powerful common scripting and
debug environment: Design for test
(DFT) logic insertion and ATPG
capabilities use a new, unified Tcl
scripting and debug environment
that is shared with the Cadence
Genus™ Synthesis Solution, the
Innovus™ Implementation System
and the Tempus™ Timing Signoff
Solution.
“Our next-generation Modus Test
Solution delivers new, innovative
patent-pending technology that
fundamentally changes the way
design and test engineers address
the test problem,” said Dr. Anirudh
Devgan, senior vice president and
general manager of the Digital and
Signoff Group at Cadence. “By using
a physically aware approach in a
2D grid, and compressing patterns
sequentially as well, the Modus Test
Solution can significantly reduce
digital test time in comparison to
traditional approaches, thereby
giving Cadence customers yet
another significant profitability
advantage.”
For more information on the Modus
Test Solution, please visit www.
cadence.com/news/modus.Samsung Launches New
LED Module Lineup, inFlux,
for High-Flux Industrial
Lighting
Samsung Electronics, a world
leader in advanced components,
introduced inFlux, a new lineup
of high-flux (extremely bright),
linear LED modules optimized
for industrial lighting applications
such as plants, parking lots and
warehouses. The LED modules
serve as a replacement for
conventional T8 and T5HO (high
output) tubes and are suitable for
high-flux LED luminaires covering
up to 40,000lm (luminous flux*).
“By providing a wide variety of
installation layout options and
brightness intensities, our new
inFlux linear module will deliver
greater design flexibility and
convenience for lighting designers,
as well as high performance and
reliability for fixture manufacturers,”
said Jaewook Kwon, Vice President,
Lighting Marketing Group, LED
Business
Team,
Samsung
Electronics. “We will continue to
reinforce our well-differentiated LED
lighting engine lineups to be able to
meet more diverse market needs.”
The Samsung inFlux LED module
incorporates the company’s mid-
power LED package (LM301A),
which features advanced “flip chip”
technology that enables a shorter
junction-to-base distance and
less thermal barrier layers in each
package, while avoiding the need
for metal wire bonding. This leads
to lowering the thermal resistance
of the packages, and permits each
package to handle a wide range of
current with improved light efficacy.