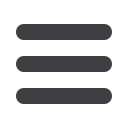

Technical article
March 2017
92
www.read-eurowire.comAs before, the fault can be located with
the well-known propagation velocity: the
result of the calculation is 758m.
DC cable (PE (for DC),
> 100kV)
The test configuration consisted of one
cable on a turntable. The cable was
connected to an adjustable DC source.
The breakdown test was performed
by using a spark gap at the far end of
the cable (
Figure 10
). The voltage was
increased until the spark gap got fired.
The resulting travelling waves were
recorded.
Parameters:
• Cable:
779m
• Capacity:
310nF/km
• Inductivity:
110µH/km
• Voltage:
up to 12 kV, DC, both polarities
• Measurement equipment:
transient recorder for fault location,
broadband divider (resistive-capacitive
attenuator) (
Figure 10
,
Figure 11
)
The same measurements as with the AC
cable were performed.
From
Equation 1
the propagation velocity
v
0
can be calculated as 171.25m/µs. With
that information the cable length
l
1
can
be determined. As a cross check the
propagation velocity
v
0
was calculated
from the measurement with the known
cable length
l
0
.
The maximum deviation from the
reference values is < 0.4 per cent.
Field Tests, Conclusions
The experimental tests have shown
the practical feasibility of the proposed
method for fault location on AC and DC
cables.
They also have shown that damping and
dispersion of the measured signal depend
strongly on the monitored cable.
Nevertheless, the experiments have been
limited to a relatively low voltage and to
a short cable length. There has been no
further knowledge about the behaviour
of cables which are laid in the soil or in the
sea.
It is assumed that the much higher
voltage during test or operation will have
a positive effect on the measured signal. It
is also presumed that the dispersion and
damping on a laid cable is lower than on
the drum or turntable.
Furthermore, the reflection losses as seen
in the measurements should not play a big
role in a real situation.
All of these assumptions are not proven so
far. Therefore, the results of the described
tests can be taken as a first step, which
has to be continued with field tests on laid
cables.
The proposed method might be helpful as
a monitoring tool during commissioning
or routine tests on long cables, but also
as an always-online tool to monitor the a
cable under service conditions.
In case of a fatal breakdown the monitored
signal shall help to find the location of
the fault in a very short time and without
further investigations.
n
References
[1]
CIGRÉ 490. Recommendations for Testing of Long
AC Submarine Cables with Extruded Insulation for
System Voltage above 30 (36) to 500 (550)kV
[2]
CIGRÉ 496. Recommendations for Testing DC
Extruded Cable Systems for Power Transmission at
a Rated Voltage up to 500kV
[3]
IEC 62067. Power cables with extruded insulation
and their accessories for rated voltages above
150kV (Um = 170kV) up to 500kV (Um = 550kV) –
Test methods and requirements
[4]
CIGRÉ 297. Practical aspects of the detection and
location of partial discharges in power cables
[5]
Leißner,
Sebastian,
Untersuchungen
zur
Fehlerortung
an
langen
HVDC-Kabeln,
Diplomarbeit, 2013
[6]
Highvolt data sheet 1.31/4, AC Capacitor, Type WC
Highvolt Prüftechnik Dresden GmbH
Marie-Curie-Straße 10
D-01139 Dresden
Germany
Tel
: +49 351 8425 700
:
sales@highvolt.deWebsite
:
www.highvolt.deVoltage kV
Cable length
l
1
with known
v
0
[m] Velocity
l
1
, with known
l
0
[m/µs]
+ 6.5
778
171.4
- 6.5
776
171.7
+ 11.5
780
170.9
- 11.5
777
171.7
▲
▲
Figure 10
:
DC cable, detail spark gap and
attenuator
▲
▲
Figure 11
:
Measurement equipment
▲
▲
Table 3
:
Calculated cable lengths and propagation velocity
▲
▲
Figure
12
:
Measurement
with
broadband
attenuator and negative DC voltage