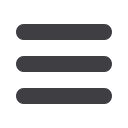

EuroWire – January 2009
38
english technology news
ABB is providing the cables for a
high-voltage connection between the
power grids of the United Kingdom and
the Netherlands. The company began
manufacturing the high voltage direct
current (HVDC) cables in August 2008 and
expects to complete the 500km of cable
needed for the contract in April 2010.
The $350 million contract was awarded
jointly by UK’s National Grid and
state-owned TenneT in the Netherlands.
The 260 kilometre BritNed link will
allow energy trading between the two
countries and increase the reliability of
electricity supplies to both.
“BritNed is another step towards an
integrated electricity network for Europe,”
said Peter Leupp, head of ABB’s power
systems division. “We are proud to
demonstrate once again that we have the
technologies needed to modernise the
European grid, stabilising supplies and
increasing capacity.”
The cables will provide a link between the
Isle of Grain in Kent and Maasvlakte in the
Netherlands. Laying of the land-based
sections was scheduled for late 2008,
while the marine cable installation is
expected to begin in April 2009. The
119mm diameter sea cables will weigh
approximately 44kg per metre and will be
installed by cable-laying vessels.
When completed, the system will have a
total capacity of 1,000 megawatts (MW)
and is expected to be in operation by the
beginning of 2011.
HVDC technology is used to transport
electrical power over long distances
with low losses using underground or
submarine cables. Power flow can be
exactly controlled and the technology also
prevents disturbances from spreading,
making a significant contribution to the
stability of the European grid.
ABB pioneered the technology in
the 1950s, when the company built
the world’s first commercial HVDC
transmission link in Sweden, and has since
supplied more than half of the world’s
HVDC projects, providing an installed
transmission capacity of more than
45,000 MW. Previous ABB HVDC projects
include the world’s longest underground
power link (in Australia) and the world’s
longest underwater connection, the
NorNed project.
ABB Ltd – Switzerland
Website
:
www.abb.comABB’s BritNed contract
Flexible flat cables (FFCs) have found
widespread use in the automotive and
IT industries. Lamination and extrusion
are the processes most commonly
used for the production of FFCs but
the disadvantage of lamination is
its extremely low production speed.
Extrusion
is
unsuitable
for
the
production of micro FFCs due to the
high temperatures and pressures
encountered in the extruder head, and
these make it impossible to maintain
accurate geometrical dimensions and
precise positioning.
Medek & Schoerner has developed
a new unpressurised cold process
for the production of FFCs using UV
cured resins, thus ensuring the perfect
geometrical accuracy of the cable at
high production speeds. The procedure
can also be employed inline with an
extruder to position the individual flat
cables accurately as they enter the
extruder head.
The same system, with some detail
modification, also allows the coating of
fine steel wire in varying colours.
Medek & Schoerner GmbH – Austria
Fax
: +43 1 982 72 96
:
m+s@medek.atWebsite
:
www.medek.atNewmanufacturing concept
for precision micro flexible
flat cables (FFC)
FFC with 12 Cu conductors 0.035 x 0.6mm
▲
▲