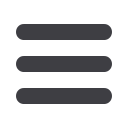

Technology News
www.read-tpt.com36
S
eptember
2015
Modular measurement gauges
for hot rolling mills
ZUMBACH Electronic has introduced
three new additions to its line of
profile gauges for steel and metal
profiles. The gauges are based on the
laser light section technique and by
camera vision, often also called the
“light cut” principle.
Up to eight line lasers “mark”
the contour of the product, and the
respective cameras each capture a large
number of pixels on the product contour.
Sophisticated software then adds four
pictures to the true, orthogonal section
of the profile. All critical dimensions,
angles and radii can be programmed
together with their tolerances.
Operators and supervisors can not
only monitor the true profile as a 1:1
section online, but also see irregular
faults such as seams, concave or
convex shapes.
All standard profiles such as H, I, U
and L beams, hexagons, squares, flats
and any special shape are measurable.
Depending on the maximum
product dimensions the three new
models cover measuring fields up to
200, 400 or 800mm.
The Profilemaster
®
delivers
accurate and stable readings,
and a high reliability is
guaranteed thanks to a
sophisticated,
multi-stage
protection and purging/cooling
system.
Key advantages include:
up to eight cameras; modular
camera setting – any shape can
be captured; up to 16,000 points/
contour (2,048/camera) = 5,734,400
points/second (with eight cameras);
high sampling rate of 350-500/second
(full profiles/second); four different
colours of laser in an eight camera
system means no interference; shape
fault detection (SFD); compilation of
a 3D model thanks to high sampling
rates; and trouble-free maintenance
with quick and easy access to the
maintenance points.
Zumbach Electronic AG
– Switzerland
Email:
sales@zumbach.chWebsite:
www.zumbach.comLarge diameter pipe mills
made in Austria by Linsinger
LINSINGER’S technology leadership,
expert knowledge and customer service
aim to provide large pipe manufacturers
with production security.
“Linsinger has continuously optimised
and improved machine performance
and this has been backed up by
high levels of R&D investment and a
balanced in-house sourcing policy,” said
Linsinger CEO Hans Knoll.
For more than 70 years Linsinger’s in-
house expertise, strict quality standards
and deadline reliability have been
valued by the large-tube industry.
Producers of large diameter pipe
require customised solutions – whether
for pipe cutting, for longitudinal seam
preparation or for pipe-end chamfering –
not only with high precision, but also with
ambitious production capacities and low
running costs.
Currently, the manufacturing of a
plate milling machine PFM 90/600LL
and a pipe end bevelling machine
RFM 56/12000 is being completed for
Haeusler, which frequently relies on
Austria-based Linsinger’s expertise.
In addition to the Linsinger KSS
sawing machines for steel billets and
the Linsinger KSA saws for seamless
tubes, the Linsinger BFMK strip edge
millers and the Linsinger MC multi-
cut parting saws have been used
successfully in longitudinally welded
pipe mills for decades. The specialised
portfolio for large diameter pipe mills
is complemented by the Linsinger
PFM plate edge milling machine and
the Linsinger RFM pipe end bevelling
machine.
The Linsinger PFM plate edge milling
machine is used for preparation of
welding edge profiles. The machine
works with height copy milling units and
is capable of maximum cutting efficiency
combined with minimum consumable
tooling costs.
Simultaneous milling of both longitu-
dinal sides saves time and money. The
profile milling tools made by Linsinger
enable virtually any geometry to be
milled with high precision and speed.
The Linsinger RFM pipe end bevelling
machine enables simultaneous cham-
fering of both pipe ends by a single
operator.
The
chamfered
pipe
surpasses API specifications and the
long tool life ensures lowest possible
running cost. The movable milling
units chamfer a range of pipe lengths
and the internal copy tools guarantee
consistent chamfer geometries.
The Linsinger RFM pipe end bevelling
machine chamfers diameters between
16" and 90" with practically no burr. The
backlash-free Linsinger patented DPD
double power drive transmission system
uses twin motors, small flanges and
high torque for absolute precision.
Linsinger Maschinenbau GmbH
–
Austria
Fax: +43 7613 8840 951
Email:
maschinenbau@linsinger.comWebsite:
www.linsinger.comProfilemaster
®
SPS 800-8K gauge