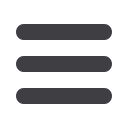

4.3. Functional Testing and Periodic Proof Testing
Another critical aspect is Functional Testing and Periodic Proof Testing, particularly because Not ALL System
Faults are Self-Revealing and Covert Faults that may inhibit SIS action on Demand can only
be detected by
testing the entire system. This requires not only a Full Functional Test prior to commissioning, typically
conducted as an integration test in the vendor or System Integrator’s facility (as well as later in the final
instrumentation room in the plant), but also Periodical Functional Tests using a documented procedures to
Detect Covert Faults and covering the entire SIS.
Functional Testing should record and analyze activation of SIS functions, and spurious activation of an
Emergency Shutdown Valve due to a Process Shut Down, but this does not test the Entire Function of the same
valve during an ESD action.
5. Automation can’t check for human intervention
Once the design is complete, all of these systems will have different degrees of interaction with users, and
different types of users with different levels of competence depending to their role (i.e. operation, maintenance
personnel and engineers)
The most sophisticated automation can’t prevent human error, industrial plants are designed with the highest
accuracy in mind, with several separate safety loops often checking the integrity of process systems. This
apparatus however can’t check for human intervention and a small human error could cause an enormous
catastrophe. 70% of reported incidents in the oil and gas industry worldwide are attributable to human error and
account for in excess of 90% of the financial loss to the industry.
Results from research conducted by the Health and Safety Executive and published in the book “Out of control:
Why control systems go wrong and how to prevent failure “[7] show the impact of the human element in
industrial incidents throughout a project lifecycle. This is shown on Figure 4.
International Functional Safety Standards (IEC 61508 and IEC61511) and previously ISA 84 introduced the
concept of the Safety Lifecycle, describing the phases that should take place from concept to design to
implementation and operation of a Safety Instrumented System. The Safety Lifecycle is a step in the direction of
reducing the impact of human factors by establishing the proper design best practices, documentation reviews
and validation and verification steps in the execution of a safety project. Additionally the standards introduce two
important elements: Competence of Personnel mentioned briefly in Section 4.2 and Functional Safety
Management System (FSMS).
Recent changes to International Functional Safety Standard IEC61508 have turned the requirements on FSMS
and Competence of Personnel into normative clauses of mandatory compliance instead of a recommendation
as was presented in the previous version of the same standard.